Our Manufacturing Standards
Our Manufacturing Standards
Unless we have agreed to other tolerances in your Quote, we will work to achieve and hold the tolerances noted below, which will vary per the primary manufacturing method you select. Rapid Manufacture has developed a comprehensive set of Design Guides to assist you in optimizing your design for the manufacturing method selected; please consult them for critical tips and tricks. In the event of a conflict between the Design Guides and this set of Rapid Manufacture Manufacturing Standards, these will control.
Workmanship Standards
Orders with Rapid Manufacture will meet the minimum workmanship standards outlined below (as applicable to the process). If your project requires a level of workmanship that goes beyond the standards listed below, please clearly list the requirement in your engineering drawings, purchase orders, or specifications.
Finished Surfaces Cosmetics
- Paint coverage on surfaces will be uniform, including adjacent materials of assemblies.
- Finished surfaces will be free of defects, including chips, scrapes, or other damage.
Mill Steps, Tooling, and Chatter
- Tool marks on as-milled surfaces will be free of defects, including burrs, chatter, tool gauges, and will meet surface roughness specifications.
- Indicated critical surfaces will be free of mill steps and marks across the entire surface.
- Milled surfaces will meet surface roughness specifications.
Chips, Burrs, and Sharp Edges
- All exposed edges will be free of burrs, sharp edges, and metal slivers.**
- **Sheet cut parts are not deburred unless specified through a selected finish.
Foreign Object Debris (FOD)
- Surfaces will be free of cutting fluid, metal chips, foreign objects, and other debris.
Threads
- Threads will be fully formed and cut to specified size and class indicated in provided drawings.
- Threads will be free of defects, notable damage, and contamination.
Plated Surfaces
- Plated surfaces will be uniform, including adjacent surfaces of assemblies.
- Plated surfaces will be free of machining marks, scratches, pits, protrusions, or visible bare metal.
- Some minor defects may be permissible in certain situations if they do not compromise the protective finish.
Weld Joints
- Weld joints are performed as indicated in the customer-provided drawing.
- Welds without specific requirements are cleaned to remove slag or other surface contamination.
- Weld joints will not be painted until the welding has been completed and the weld has passed inspection.
Countersinks
- Countersinks shall be round and made to print specifications and allow the proper designed fit with the mating screw.
- Countersinks will be free of burrs, chatter, or other tooling defects.
Painted Surfaces
- Painted surfaces shall be consistent and continuous in the finish.
- Painted surfaces shall be free of visible machining marks, scratches, abrasions, dust particles, fisheyes, orange peel, or bare metal.
- Painted surfaces should be reviewed against this standard at a distance of 18″ at 1X magnification.
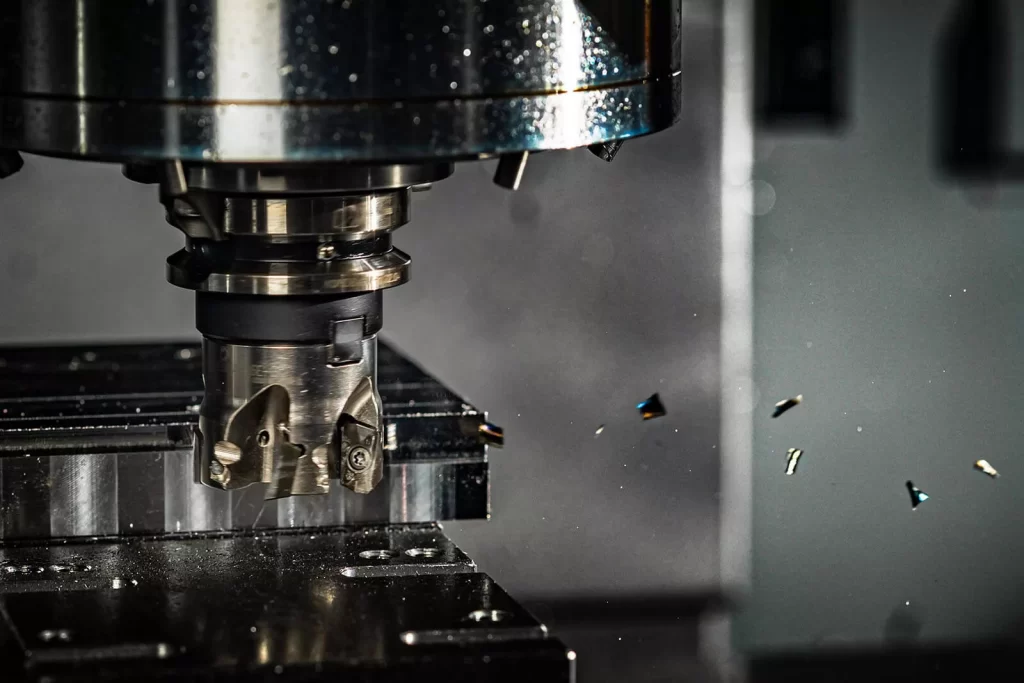
CNC Machining and Turning
- For features of size (Length, width, height, diameter) and location (position, concentricity, symmetry) +/- 0.005” (metals) or +/- 0.010 (plastics and composites) following ISO 2768 unless otherwise specified.
- As machined surface finish is 125 Ra or better. Machine tool marks may leave a swirl-like pattern.
- Sharp edges will be broken and deburred by default. Critical edges that must be left sharp should be noted and specified on a print.
- Clear or transparent plastics will be matte or have translucent swirl marks on any machined face. Bead blasting will leave a frosted finish on clear plastics.
- Xometry cannot guarantee tolerances on foam or similar compressible materials.
- General tolerances for orientation and form features are outlined below unless we have agreed to other tolerances in your Quote. These features include parallelism, perpendicularity, cylindricity, flatness, circularity, and straightness.
CNC Orientation and Form General Tolerance
Table: Parallelism, Perpendicularity, Cylindricity, Circularity, Flatness, and Straightness over Part Length
Part Length | Orientation and Form Tolerance | Angularity Tolerance |
---|---|---|
0 to 12″ | +/- 0.005″ | Angularity +/- ½ degree |
12″ to 24″ | +/- 0.010″ | Angularity +/- ½ degree |
24″ – 36″ | +/- 1/64″ (0.016″) | Angularity +/- 1 degree |
36″ – 60″ | +/- 1/32″ (0.031″) | Angularity +/- 1 degree |
Over 60″ | +/- 1/16″ (0.063″) | Angularity +/- 1 degree |
Die Casting
- Typical mold machined tolerances are +/- 0.010″ when machining the mold and an additional +/- 0.001″ per in. when calculating shrink rate.
- Tighter as-molded tolerances can be requested and may increase the cost of tooling. Additionally, many tight tolerances require the mold to be manufactured, sampled, and groomed. Xometry will mill to a steel-safe condition on critical features.
- Critical toleranced features and surface finishes may require post-machining and should be noted in the quote prior to order. Post-machined features will follow Xometry’s CNC manufacturing standards.
- Xometry will produce die cast components according to the net-shape (as-cast) model provided by the customer. These models must contain appropriate material for any additional post-processing efforts, such as post-machining. It is recommended to provide the as-cast 3D model as well as the final model with any accompanying technical drawings.
- Part-to-part repeatability is typically under +/- 0.004″.
- As-cast surface finish is typically 64 μin. The standard finish for die-casting is as-cast and cannot guarantee a specific Ra value without additional processing.
- The lead time is for the first article shipment (T1 shipment). The remaining production time is confirmed after the first article approval.
- Typical first article shipments are five pieces but may vary based on size, origin, and material.
- All quotes are based upon the assumption that designs have an adequate draft, radii, and coring for manufacturability.
- Cores, side actions, and tooling strategy are determined by Xometry unless explicitly discussed.
- Gating, ejection, knit lines, and parting lines are at the discretion of Xometry unless explicitly discussed.
- Parting line(s) on die cast parts will be visible as a thin ridge traveling across the part.
- Cast parts may have one or many gate vestiges, which are trimmed, sheared, or ground off.
- Ejector pin marks will be present on die cast parts, resembling round flats.
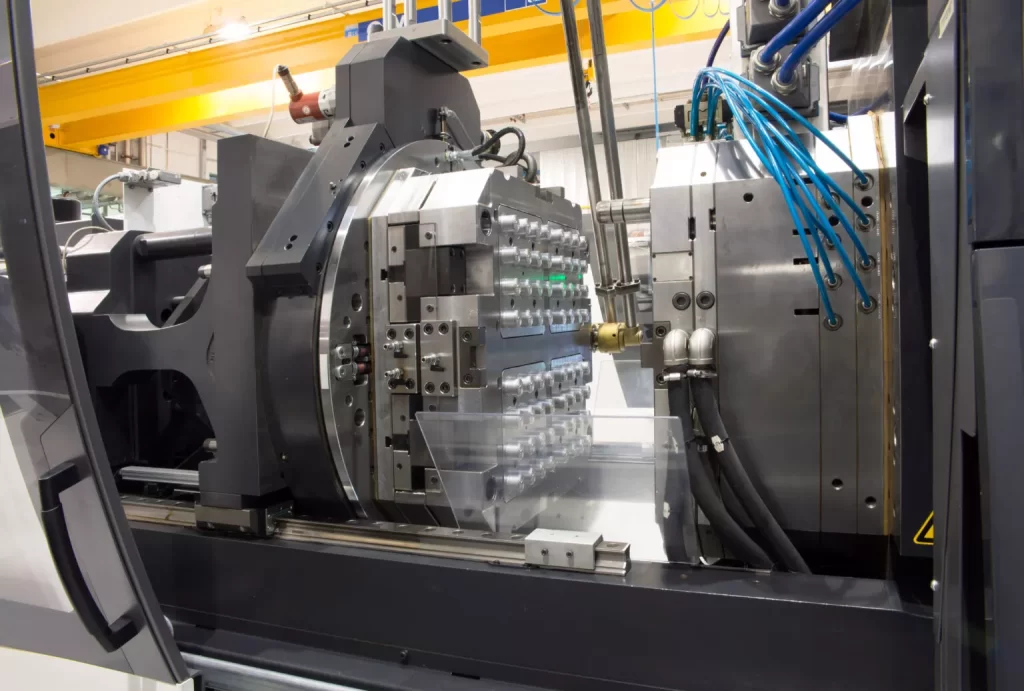
Plastic Injection Molding
- Typical mold machined tolerances are +/- 0.005″ when machining the mold and an additional +/- 0.002″ per in. when calculating for shrink rate.
- Tighter tolerances can be requested and may increase the cost of tooling. Additionally, many tight tolerances require the mold to be manufactured, sampled, and groomed. Xometry will mill to a steel-safe condition on critical features.
- Part-to-part repeatability is typically under +/- 0.004″.
- Lead time stated is for first article shipment. Remaining production time is confirmed after first article approval.
- Typical first article shipments are 10 pieces but may vary based on size, origin, and material.
- Xometry cannot guarantee a perfect color match per Pantone color.
- All quotes are based upon the assumption that designs have an adequate draft, radii, and coring for manufacturability.
- Cores, side actions, and tooling strategy are determined by Xometry unless explicitly discussed.
- Gating, ejection, knit lines and parting lines are at the discretion of Xometry unless explicitly discussed.
Sheet Cutting Service
- Thickness tolerances are independent of cutting tolerances, as they rely on the raw stock material’s tolerance range.
- Edge to edge tolerances is +/- 0.010” nominal on the top face of the plate/sheet.
- Thicker materials may have a tolerance deviation on the bottom face due to tapers inherent in laser cutting, waterjet cutting.
- Xometry cannot guarantee flatness call outs for sheet cut materials except on ground stock or tooling plate (e. g. MIC6).
- Holes of 0.100” or smaller in diameter may be slightly larger on the top face than standard tolerances due to the cutter piercing the material near the hole’s cut line.
- A small bump or divot in the material or a different edge condition may be present at the lead-in and lead-out in a cutting profile.
- Pre-finished or textured sheets, such as brushed or polished stock may have only one side with the cosmetic finish.
- Protective film may be shipped on cut products to prevent damage of cosmetic finishes.
- The edge condition of sheet cut materials will have vertical striations versus smooth edges. This affects the transparency of edges on clear plastics cut with waterjet.
- Some cut materials may show a small halo discoloration from backsplash (waterjet) or overspray near the cut edges (laser).
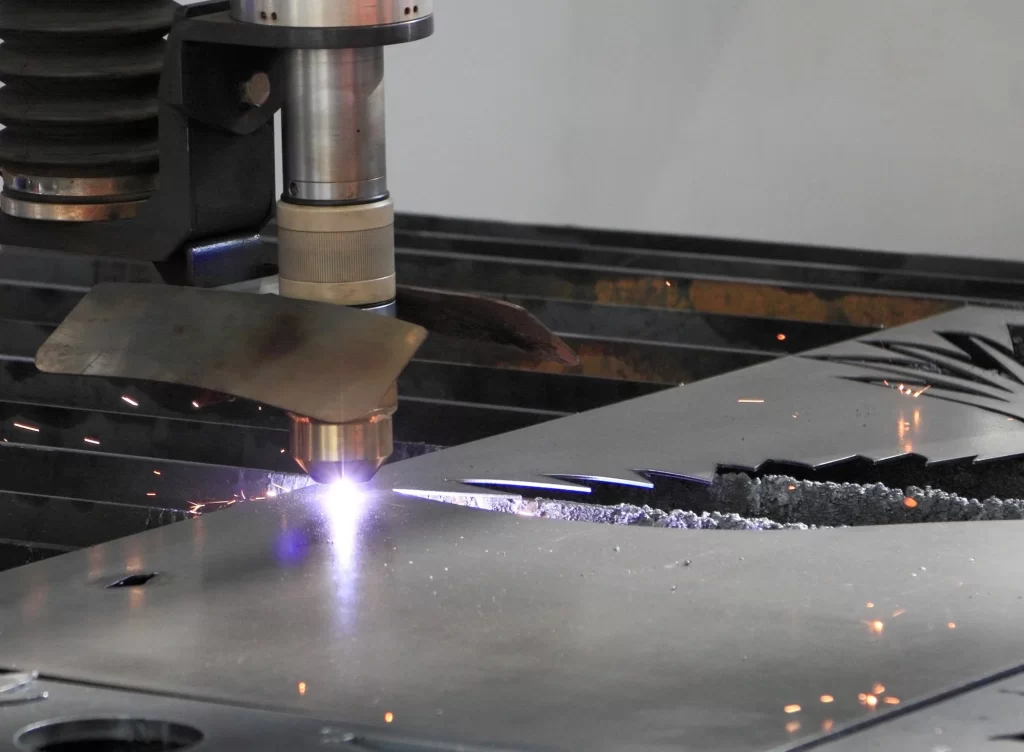
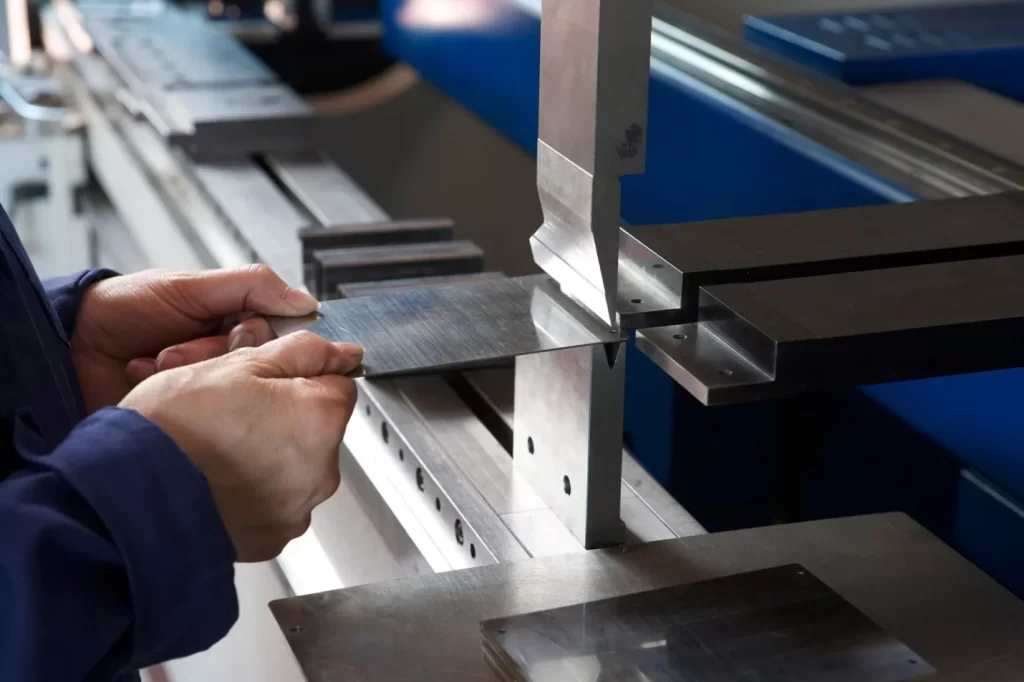
Sheet Metal Fabrication
- Forming and bending: +/- 0.030″
- Bend to hole or feature: +/- 0.010″
- Linear dimensions excluding locations to bends: +/- 0.010″
- Angularity: +/- 2 degrees
- Surface roughness (blank material): Ra 125 uin max
- Surface roughness (timesave): Ra 100 uin max
- Sharp edges will be broken and deburred by default. Critical edges that must be left sharp should be noted and specified on a print.
- Specific sheet metal designs require custom tooling and will be flagged for a manual quote: hems, curled flanges and rolled sheets, stamped parts, and welded assemblies. If your part includes these features, please allow our manual quote team to review and provide you with an accurate cost and lead time.
Sheet Metal Tolerances Reference Table
Dimension Detail | Tolerance | Image Reference |
---|---|---|
Edge to Edge, Single Surface |
+/- 0.010″ |
A |
Edge to Hole, Single Surface |
+/- 0.010″ |
B |
Hole to Hole, Single Surface |
+/- 0.010″ |
C |
Hole Diameter, Single Surface |
+/- 0.010″ |
D |
Bend to Edge / Hole, Single Surface |
+/- 0.010″ |
E |
Edge to Feature, Multiple Surface |
+/- 0.030” |
F |
Over Formed Part, Multiple Surface |
+/- 0.030” |
G |
Bend Angle |
+/- 1 deg |
H |
Metal Stamping
- All quotes are based upon the assumption that designs have an adequate draft, radii, relief cuts, and feature sets for manufacturability in this process.
- Critical-to-function tolerances should be discussed at the time of quoting to ensure that tooling strategy, check gages (if applicable), and other quality controls are encompassed in the quote.
- Raw material such as coiled strip is not flat by nature and can show through on flat stamped or coined components.
- Dimensions apply to the inside of the formed feature.
- Angular tolerances of +/- 1 degree are typical.
- Stamped parts will be free of splits and other forming defects.
- Punch and die-cut features, such as edges, will have a straight wall with a small burr on the bottom edge approximately ¼ to ⅓ down the wall thickness.
- Large burrs and tabs will be removed, but parts are not manually fully deburred before shipment with a standard, as-cut finish selection.
- Linear dimensions for internal holes will be measured at the shear, or smallest portion of a cut feature.
- Tooling marks are a normal part of the metal forming process. Marks can be minimized with secondary processing or tooling strategy. It is important to identify cosmetic features with Xometry during the quoting or kick-off phase.
- The material thickness will vary across formed and drawn features.
- Part-to-part repeatability is typically under +/- 0.004″ (+/- 0.002” typical).
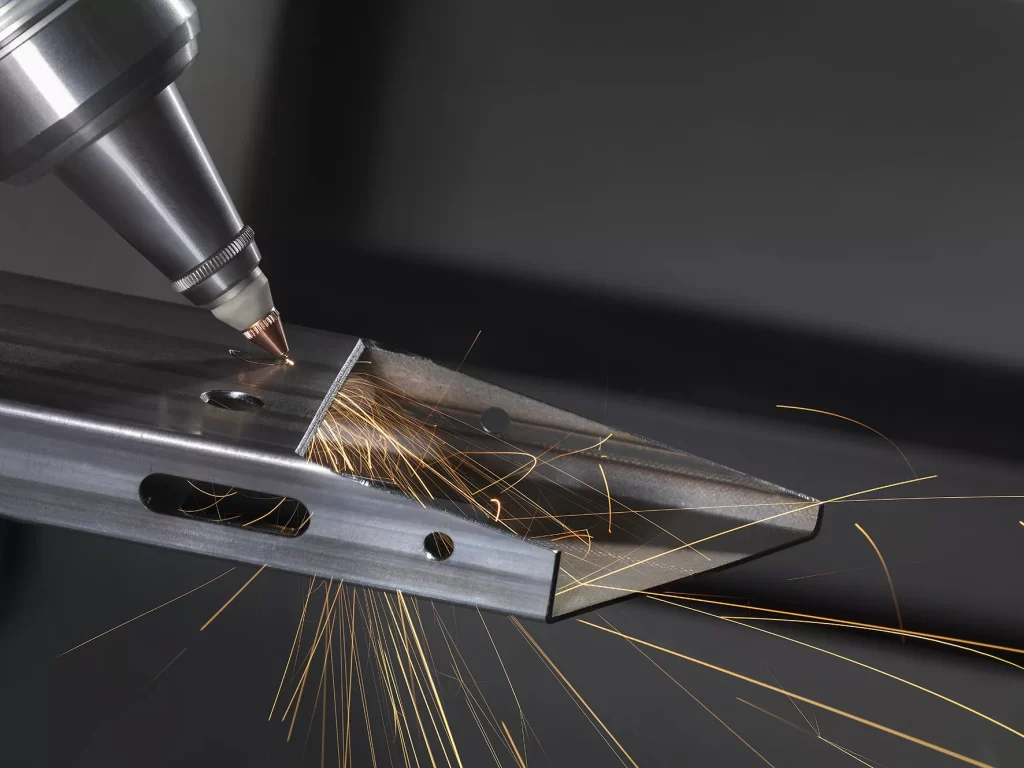
Laser Tube Cutting
- Thickness tolerances are independent of cutting tolerances, as they rely on the raw stock material’s tolerance range.
- Edge-to-edge tolerances are +/- 0.010” nominal on the outer face of the tube.
- Thicker materials may have a tolerance deviation on the bottom face due to tapers inherent in laser cutting.
- Holes of 0.100” or smaller in diameter may be slightly larger than standard tolerances due to material pierce happening near the hole’s profile
- A small bump of material or a different edge condition may be present at the lead-in and lead-out in a cutting profile.
- A protective film may be shipped on cut products to prevent damage to cosmetic finishes.
- Large burrs and tabs will be removed, but parts are not manually fully deburred before shipment with a standard, as-cut finish selection.
- Some cut materials may show a small halo discoloration from the backsplash or overspray near the cut edges.
Tube Bending
- Tube bending manufacturing standards reflect draw or mandrel bending techniques. Compression bending, roll bending, or other bending methods will require functional specifications agreed upon at the time of order.
- Thickness tolerances are independent of cutting tolerances, as they rely on the raw stock material’s tolerance range. Tolerance measurements will assume a maximum material condition of the stock.
- Overall tube sheath envelope tolerance is +/- 0.125” typical.
- Tolerances are cumulative across bent tube feature.
- Linear dimensions excluding locations to bends: +/- 0.010″.
- Simple bend, planar, +/- 0.010”.
- Multiple surface bends, multi-planar, +/- 0.030”.
- Angularity: +/- 2 degrees.
- Tube end diameter tolerancing is +/- 0.020”.
- Ovality at a tube bend should not exceed 10% (5% to 8% typical) of averaged measured OD vs.. nominal OD. The equation for ovality is ((Max Ø – Min Ø) ÷ specified Ø) x 100.
- Thicker materials may have a tolerance deviation on the bottom face due to tapers inherent in cutting.
- Holes of 0.100” or smaller diameter may be slightly larger than standard tolerances due to material near the hole’s profile.
- A small bump of material or a different edge condition may be present at the lead-in and lead-out in a cutting profile.
- A protective film may be shipped on cut products to prevent damage to cosmetic finishes.
- Large burrs and tabs will be removed, but parts are not manually fully deburred before shipment with a standard, as-cut finish selection.
- Some cut materials may show a small halo discoloration from the backsplash or overspray near the cut edges.
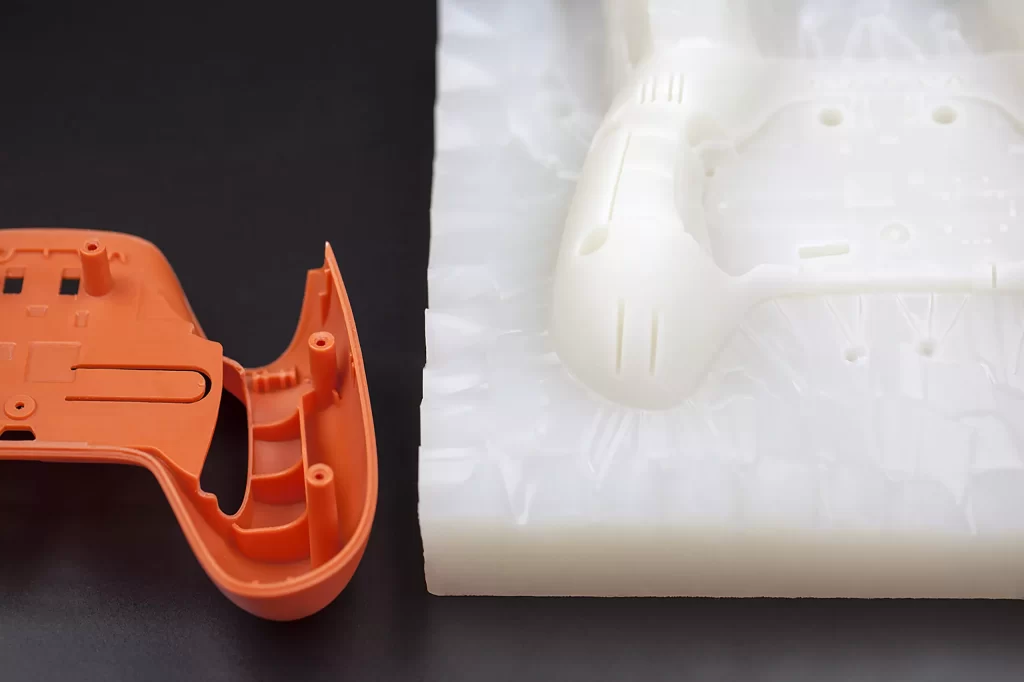
Urethane Casting
- Tolearance are +/- 0.010” or +/- 0.003” per inch, whichever is larger, is typical. Irregular or overly-thick geometries may cause deviances or deflection due to shrinkage.
- A shrinkage rate of +0.15% can be expected due to thermal expansion of the liquid, and the response of the flexible mold.
- Surface finish is externally smoothed to a satin or matte surface. Grow lines may be present on internal or difficult-to-access features. Polishing or custom finishes must be clearly defined and agreed upon at the point of order.
- Sharp corners and text may appear slightly rounded.
Nexa3D LSPc® 3D Printing
- +/- 0.005” in the XY-plane and +/- 0.010″ in the Z-plane for the first inch is typical, plus +/- 0.002” for every inch thereafter. However, Xometry does not guarantee tolerances on the first order of a new design.
- Tolerance expectations can vary across different materials (e.g., elastomeric versus rigid materials). Tolerances on flexural materials, such as xFLEX or xPP405, cannot be guaranteed on the first run.
- General tolerances apply before secondary finishing or post-processing unless otherwise specified. Guaranteed tolerances may be possible with a manual quote review, and must be approved on a case-by-case basis.
- Upward facing surface may experience 0.010-0.020″ of additional growth due to required support style for printing.
- Modeled threads or precision features may have limited functionality as printed. Tapping or the addition of threaded inserts is recommended for best function.
- Some materials, such as xCE, may become translucent in thin walled sections. Clear materials, such as xMODEL17, will print with a frosted-like appearance and are not typically suitable for applications requiring optical clarity.
- Some materials, such as “xFLEX” materials, may exhibit off-gassing or an odor which may lessen over time.
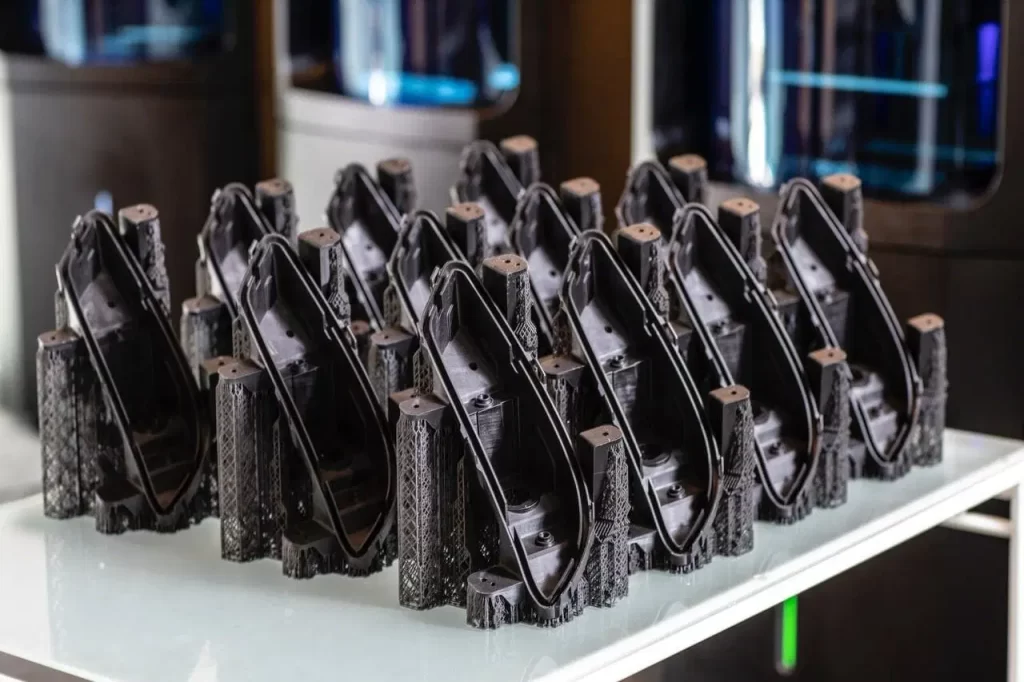
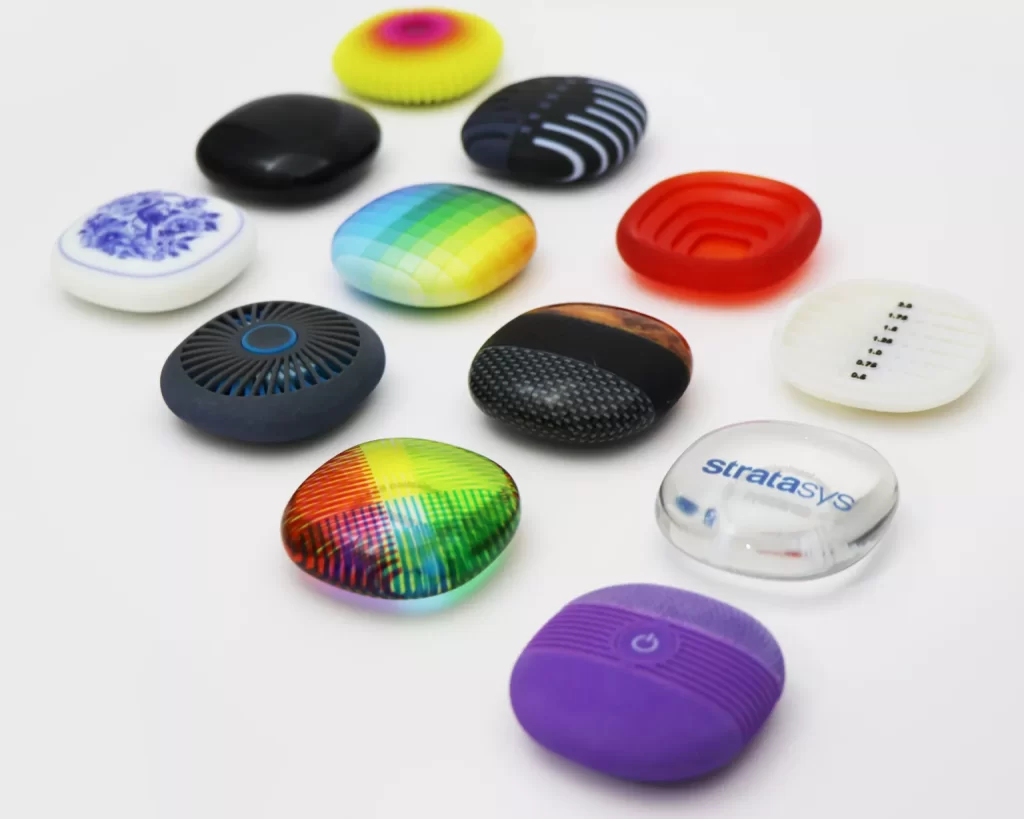
Polyjet 3D Printing
- +/- 0.004” for the first inch is typical, plus +/- 0.002” for every inch thereafter.
- Minimum feature size of 0.050” can be built with consistency.
- Rubber-like materials represent an approximation of shore A values and may vary between geometries.
- General tolerances apply before secondary finishing or post-processing unless otherwise specified.
SLA 3D Printing
- Guaranteed tolerances may be possible with a manual quote review, and must be approved on a case-by-case basis.
- Modeled threads or precision features may have limited functionality as printed. Tapping or the addition of threaded inserts is recommended for best function.
- Tolerances for Standard and High Resolution options are described in the table below
- General tolerances apply before secondary finishing or post-processing unless otherwise specified.
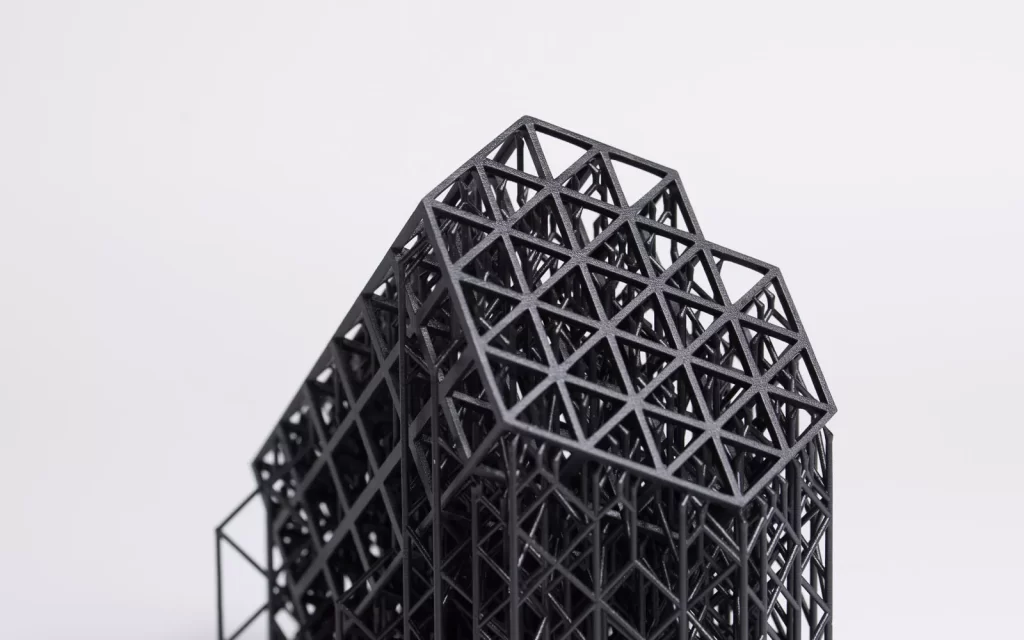
Tolerances for SLA, Standard and High Resolution
Feature | Standard Resolution | High Resolution |
---|---|---|
Tolerance, XY Plane |
+/- 0.005” for the first inch is typical, plus +/- 0.002” for every inch thereafter. |
+/- 0.005” for the first inch is typical, plus +/- 0.002” for every inch thereafter. |
Tolerance, Z Plane |
+/- 0.010” for the first inch is typical, plus +/- 0.002” for every inch thereafter. |
+/- 0.010” for the first inch is typical, plus +/- 0.002” for every inch thereafter. |
Minimum linear feature size |
Under 0.030” are at risk and under 0.020” will not build. |
Under 0.020” are at risk and under 0.010” will not build. |
Minimum radial feature size |
0.035″ |
0.030″ |
Layer height |
0.004″ |
0.002″ |
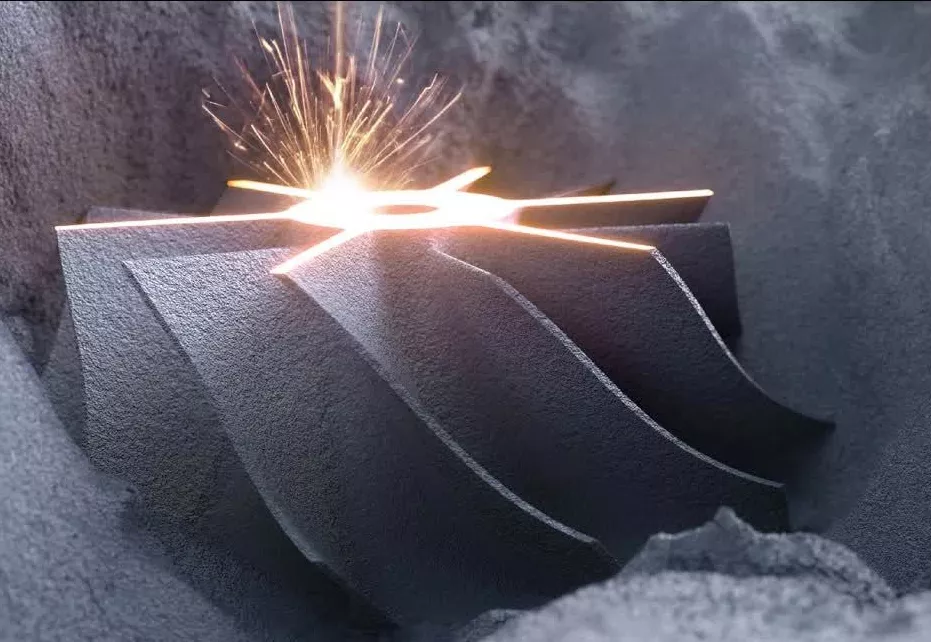
SLS 3D Printing
- +/- 0.010” for the first inch is typical, plus +/- 0.002” for every inch thereafter is typical for most materials. Nylon 12 CF +/- 0.015” for the first inch is typical, plus +/- 0.002” for every inch thereafter.
- Parts with thicker geometries, flat or broad parts (>7”), and parts with uneven wall thicknesses will be prone to significant deviations or warp due to variable thermal shrinkage and stress.
- Modeled threads or precision features may have limited functionality as printed. Tapping or the addition of threaded inserts is recommended for best function.
- Guaranteed tolerances may be possible with a manual quote review, and must be approved on a case-by-case basis.
- General tolerances apply before secondary finishing or post-processing unless otherwise specified.
- Standard size holes will be drilled out if accessible, holes smaller than 0.040″, irregular, or deep holes may shrink or sinter shut.