Selective Laser Melting (SLM) Service
Selective Laser Melting (SLM) 3D Printing precisely constructs metal parts by sintering metal powder with strong laser beams at fine resolution. Tap on this incredible technology and easily manufacture complex metal prototypes and functional end use parts.
SLM 3D printed parts manufacturer
From prototyping to small-batch production, our global network of certified SLM 3D printing facilities will allow you to produce highly accurate parts with quality and strength comparable to injection molding.Our expertise in additive manufacturing, high-end functional testing prototypes, 24 hours services, competitive price, on time delivery drop- shipping to over 150 countries to help you transform your ideas into projects, bring your innovative products to market faster, reduce your production costs, save your research and development time.Upload your CAD files, receive an instant Selective Laser Melting 3D printing quote and get your parts into production in less than 5 minutes.
Get an Instant Quote Online
Upload your 3D CAD model and get an instant quote using our proprietary digital manufacturing platform. Whether aluminum, stainless steel, tool steel or titanium – we’d be happy to advise you on the advantages of 3D printing metal parts!
Different options of metal materials available to be printed with SLM
- Tool Steel H13
- PtRh20
- Invar 36
- Gold
- Copper
- SLM 1.2709
- many more
- Ti6Al4V
- IN 718
- Scalmalloy RP
- AMZ4
- Heraeus Ptlr50
- AlSi10MG
- Stainless Steel 316L
Design guidelines for SLM
Minimum Build Size |
5mm*5mm*5mm |
Maximum Build Size |
250mm*250mm*292mm |
Recommended wall thickness |
1.5mm |
Minimum Embossed & Engraved Details |
1.0 mm deep & 1.0 mm wide |
Minimum Clearance (between parts that will be assembled together) |
0.2mm |
Minimum Clearance (between two moving or connecting parts) |
1.0mm |
Threads Design |
Thread pitch – 1.0mm |
Minimum Escape Hole Diameter |
2.5mm |
Minimum Holes design |
1.5mm |
Minimum column design |
1.5mm |
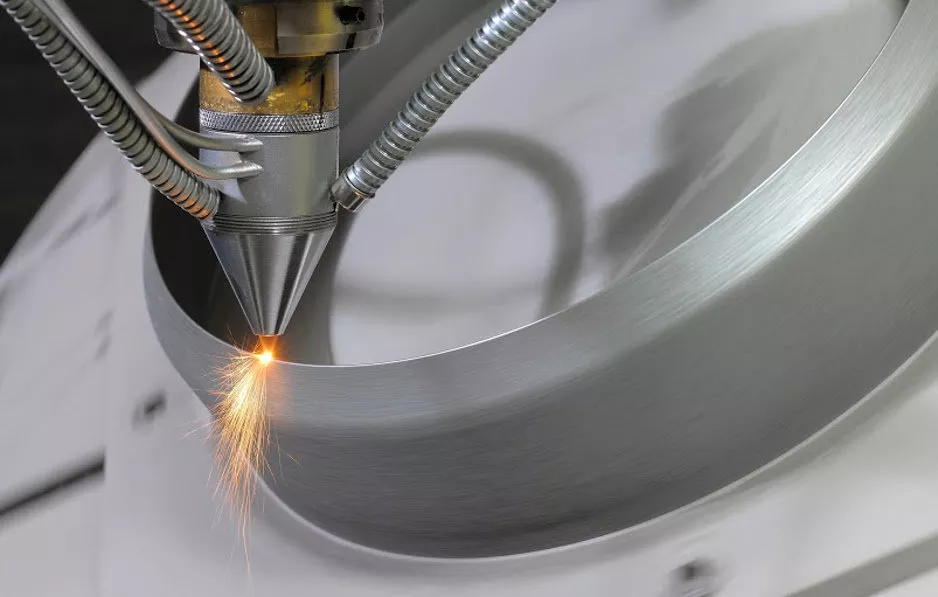
What Is SLM 3D Printing?
SLM is a promising 3D printing technology for metal parts. SLM molding materials are mostly single-component metal powders, including austenitic stainless steel, nickel-based alloys, titanium-based alloys, cobalt-chromium alloys, and precious metals. The laser beam quickly melts the metal powder and obtains a continuous melt channel, which can directly obtain nearly dense metal parts with almost any shape, complete metallurgical bonding, and high precision. Its application range has been extended to aerospace, microelectronics, medical, jewelry and other industries. The main defects in the SLM molding process are spheroidization and warpage deformation.
How Selective Laser Melting 3D Printing Works
SLM is based on a cyclical process in which the process is repeated until the production run is completed: The printing machine spreads an even layer of powdered metal on the build platform. The powder is then fused by a high-powered laser into a desired form. When the form is ready the production machine lowers the build platform according to the layer thickness and spreads a new layer of powder which is again fused by the laser. The process is repeated until the production run is ready. The diameter of the laser beam is extremely small which makes it possible to produce complex forms.
When in print mode the parts require support structures. The supports are used in metal printing to support the parts while printing and also for conducting the heat away from the body. The supports are printed with the parts connecting the parts to the printer’s build platform.
The excess powder from the production run can be re-used through sieving. Other post processing procedures include annealing the printed parts, removing the support structures, and enhancing the surface quality with glass-bead blasting. Also polishing, electropolishing, and machining are common post processing procedures.
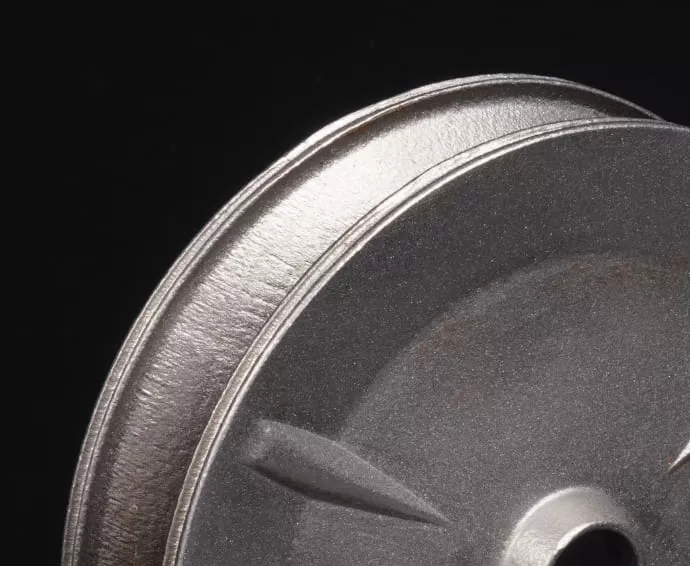
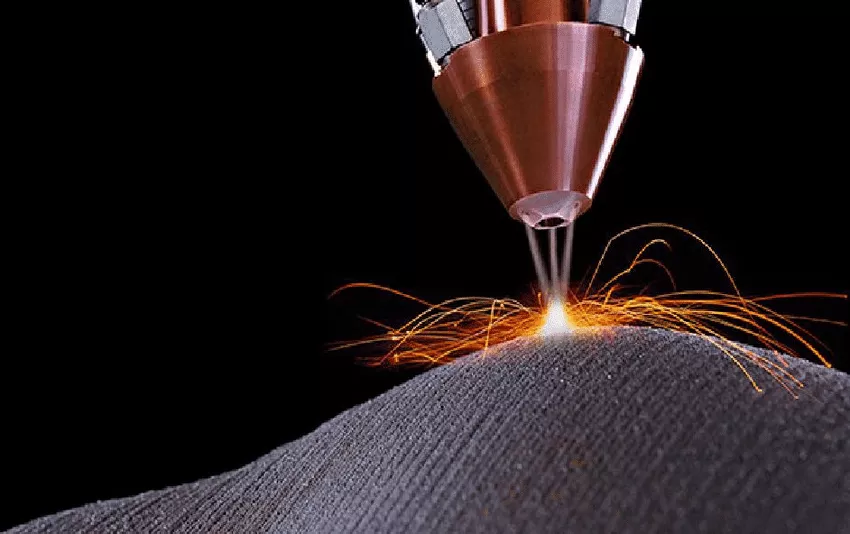
Why Choose SLM Technology?
- Targeted lasers melt individual thin layers of metal alloy powder to create heat resistant parts in one step with fine details, no matter the design’s geometric complexity.
- On-demand, unified parts produced with reduced cycle time, ideal for prototyping or low-volume production.
- Material options to align with any industry, design requirements, all with reduced assembly time.
- Allows for part consolidation, reducing assembly time, and reduced part weight.
Main advantages of SLM
1. The density of metal parts formed by SLM is high, which can reach more than 90%;
2. The mechanical properties such as tensile strength are superior to those of castings, even reaching the level of forgings. Vickers hardness can be higher than that of forgings;
3. Because it is completely melted in the printing process, the dimensional accuracy is high;
4. Compared with traditional material reduction manufacturing, it can save a lot of materials.
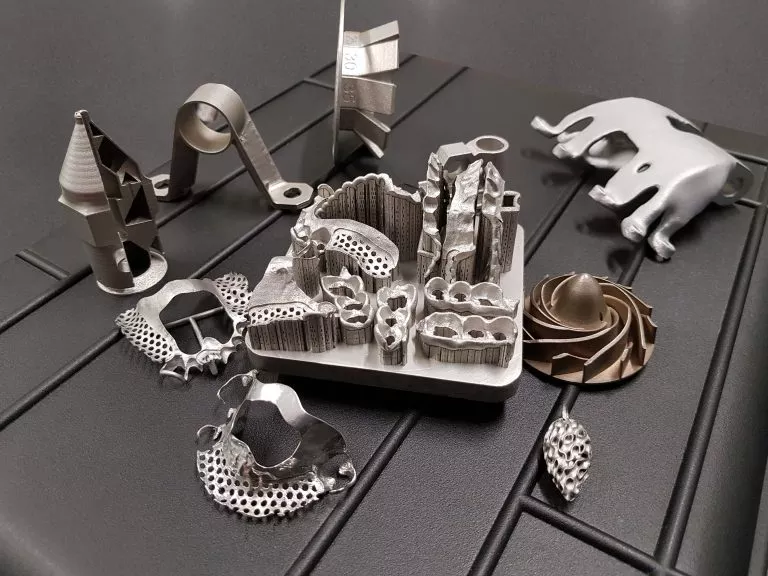
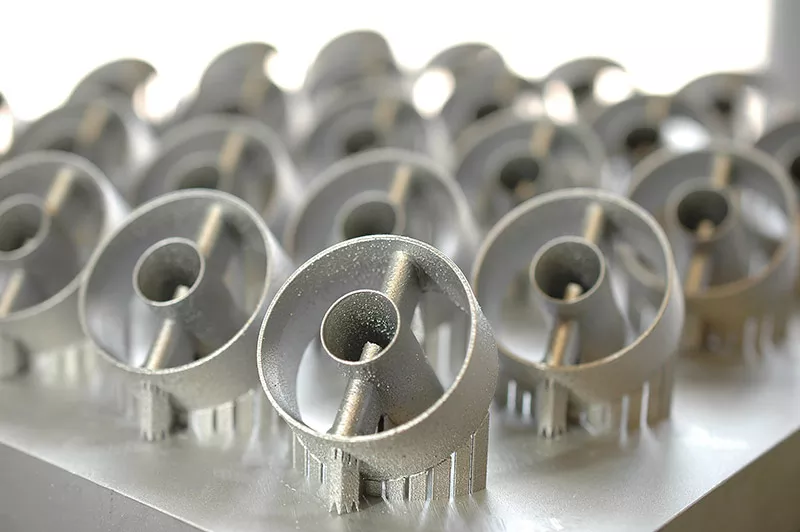
Applications
- Prototypes, pilot series, small batches
- Individual parts / obsolete components
- Lightweight construction / bionic lightweight design
- Medical technology, dental technology
- Aerospace
- Toolmaking, machine tool manufacturing, plant engineering
- Automotive and racing
- Oil and gas industry
- Energy industry
Upload CAD files and get prices
Take advantage of this opportunity to choose the right properties for your components from over 100 different materials and take advantage of the benefits of 3D printing. We provide you with our factory and unique material selection guide. Here you will find alternatives to current materials and improve the performance of your products.