Selective Laser Sintering (SLS) 3D Printing Service
Selective Laser Sintering (SLS) is a 3D Printing technology that is ideal for producing industrial strength parts on demand.Upload your CAD file to get instant quotes on SLS parts.
SLS printing is perfect for many of your rapid prototypes, low- and mid-volume productions, and functional testing
Selective laser sintering 3d Printing is very good for producing prototypes which require strength. It consists of functional plastic part which contains mechanical properties and used in prototyping or low volume production.
Selective Laser Sintering (SLS) is a 3D printing technology used to combine tiny particles of plastic powder (nylon and carbon fibre) with laser technology to produce a solid object. We offers the best SLS 3D printing service that has become the most chosen printing technology amongst the industries dealing in consumer goods, factory tools, aerospace components, and more.
We’ll create your 3D printed parts accurately according to your original object and deliver within the time we committed. Let us serve you!
Try our Selective Laser Sintering (SLS) 3D Printing Service
Rapid Manufacture creates your exact designed product with their SLS 3D printer service. Just upload your CAD drawings to our instant quotation system and the system will give you a quotation immediately, or send us a message through the contact page and we will give you a quick quotation.
SLS Capabilities
SLS is an additive manufacturing technology that uses a laser to fuse particles of plastic powder together building parts layer by layer. This powder bed technology rivals injection moulding prices for short production runs of small parts. SLS technology has hardly any printing limitations giving freedom to design and print complex geometries.
Maximum Printing Size | 350*350*400mm |
Lead Time | 48 hours or 72 hours |
Tolerance | ± 300μm or 0.3%mm |
Minimum Layer Thickness | 0.8 mm |
Applications of SLS
Concept Models: Because SLS can be used to produce complex shapes with fine detail, it’s a preferred technique for creating concept models.
Rapid Prototypes: Producing parts in SLS is fast and affordable. That makes it an excellent choice for new product innovation and rapid iteration of prototype parts. Additive manufacturing can help you avoid the expense of reworking, or even worse, completely scrapping an expensive mold.
Bridge Production: Tooling lead times for large injection molded parts tend to be quite long. SLS parts can be used to fill the gap until your tools are available.
Durable Production Parts: The isotropic strength of SLS parts gives them excellent mechanical strength in a variety of demanding applications.
Mass-Customized Parts: SLS makes it easy to simultaneously produce multiple versions of a prototype part design, or to customize part designs and quickly produce new part variations to meet fast-changing customer needs.
Industries Where SLS parts are Used Include: Medical devices, aerospace parts, automotive components, and manufacturing
Ready to Get Started?
From design to prototype and production, our team of engineers is ready to help bring your idea to life with Selective Laser Sintering (SLS) 3D printing.
What is Selective Laser Sintering (SLS)?
Selective Laser Sintering (SLS) is an industrial additive manufacturing process that fuses together powdered thermoplastic polymers using a high powered laser. The laser selectively sinters the particles of the powder and binds it together to create a solid structure, layer by layer. SLS offers fantastic part throughput with its unique ability to nest thousands of parts within the boundaries of the machine without the need for support structures. This allows it to be used not only for rapid prototyping, but also for high volume manufacturing of end-use parts. SLS offers 5 high performance 3D printed materials that offer durability, electric static dissipation, temperature resistance, USP Class VI Biocompatibility, and/or Flame, Smoke Toxicity (FST) UL-94 ratings.
Manufacturing using Selective Laser Sintering 3D printing services is ideal for producing parts that look, feel and perform like end-use parts. They offer a uniform matte finish with little to no visible layer lines. Functionally they perform exceptionally well in demanding applications, offering consistent mechanical properties, abrasion resistance and excellent impact resistance. This makes SLS 3D printing a great substitute for injection molding or functional rapid prototyping at low to mid sized production volumes.
6 Easy Steps For Making Parts In SLS
- The powder is dispersed in a thin layer on top of a platform inside of the build chamber.
- Preheats the powder to a temperature just below the melting point of the raw material.
- Laser scans a cross-section of the 3D model, heating the powder to just below or right at the melting point of the material.
- Build platform lowers by one layer into the build chamber, and a recoater applies a new layer of powder material on top. The laser then scans the next cross-section of the build until parts are complete.
- Cooldown the part, move the powder, sand-blasting the surface to make it smooth.
- Dyeing or painting to get more colors
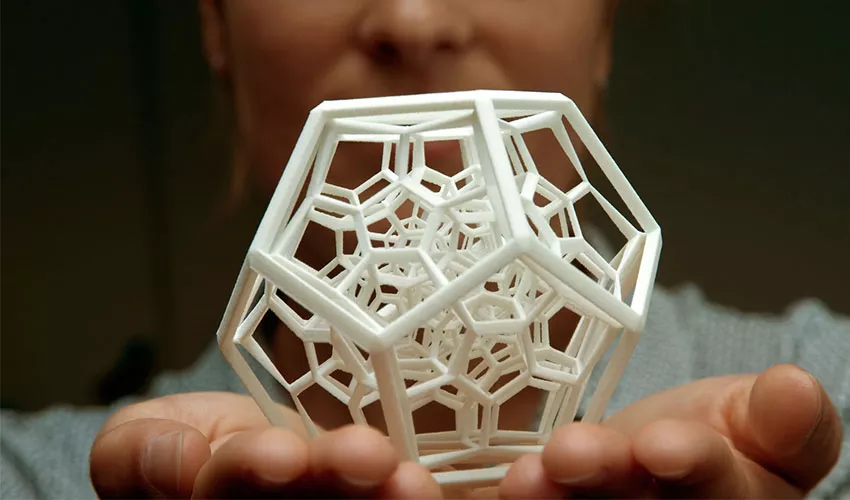
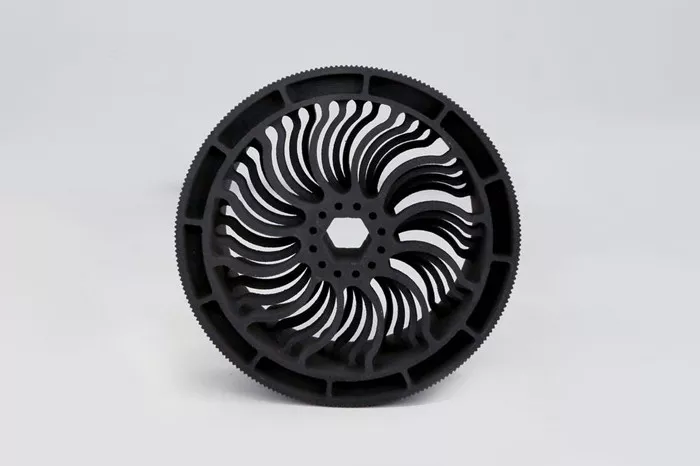
What materials are used in selective laser sintering?
Selective Laser Sintering is limited to thermo-plastic resins, as opposed to thermo-set resins. Basically, the particles in these polymers are melted together or fused by the laser.
Typically for SLS, nylon-based resins are used, commonly including:
- Nylon-12
- Nylon-6
- Nylon-11
- Composite nylons
- Carbon-filled nylon
- Glass-filled nylon
- Aluminum-filled nylon
- Glass fiber-filled nylon
SLS Post-processing
We provide a wide range of post-processing options, making it possible to achieve the desired outcome.
Get painted according to the color pattern provided by the customer (Including matte paint, high-gloss paint, electroplating-imitation paint, varnish, leather paint,etc).
The surface texture is polished in a variety of ways to meet the actual needs of customers. The transparent parts can be polished accordingly to improve transparency and light transmittance.
Provide electroplating services, improve the overall strength of the parts, provide metal-like surface texture, and make it have certain metal characteristics.
At the specific bottom hole position that needs to be processed, the internal thread is processed.
The surface of the part is glazed to better imitate the appearance of handicrafts. Have mature assembly experience to ensure the overall display of the product.
The unique outer coating processing ability improves the strength of the product structure, reduces external wear, and can better avoid damage caused by normal storage and use.
A variety of measuring equipment provides reasonable measure services according to the actual needs of customers.
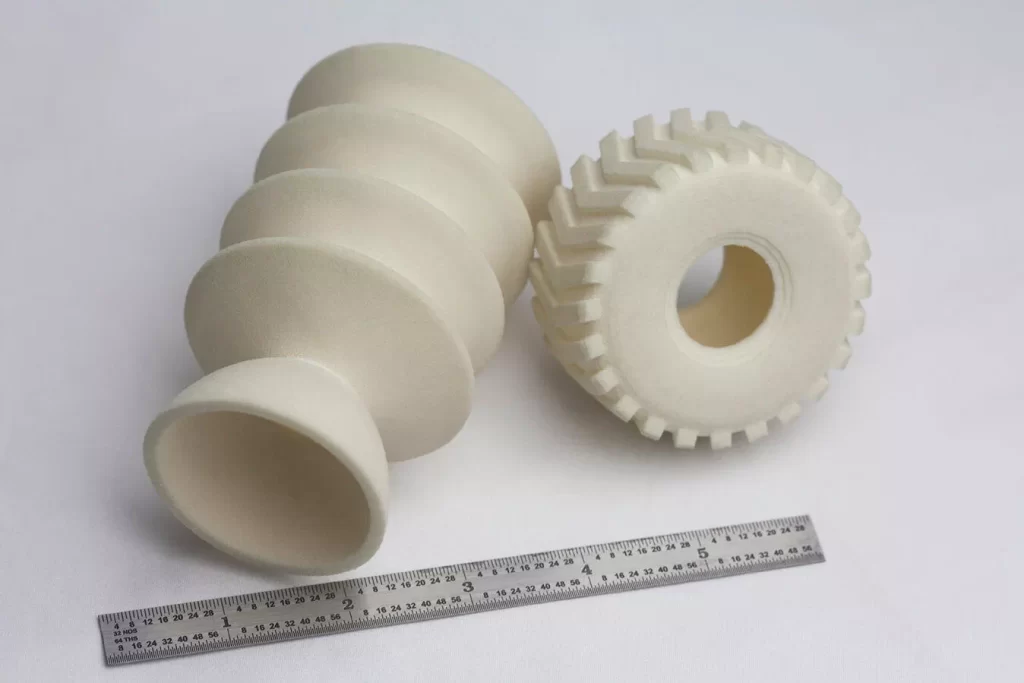
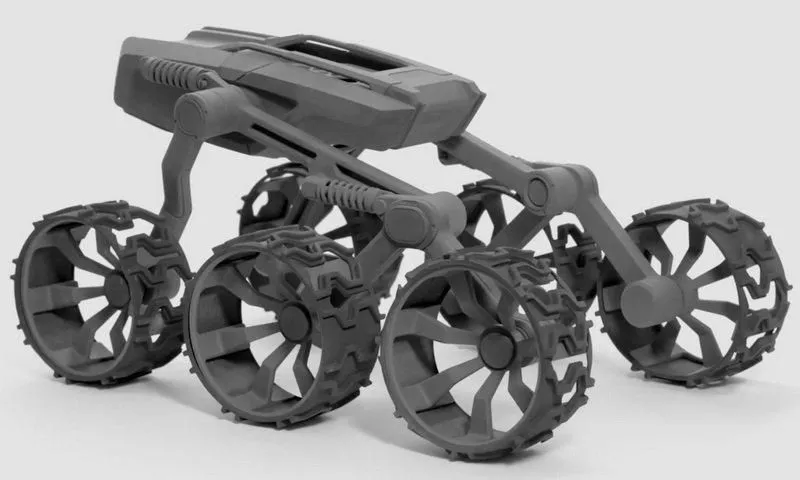
Advantages of SLS 3D Printing
There are many advantages to using SLS 3D printing, which make Selective Laser Sintering popular among engineers & manufacturers. SLS 3D printing is fast, enabling high productivity. And the parts produced use strong adhesives, enabling complex shape production which can be easily dyed or coloured.
- Great for functional parts and prototypes
- Complex geometries
- Low volume production possible
- Rapid production
- High strength material
- Fast and flexible
Design guidelines for SLS
Features | Recommended Size |
Minimum Build Size | 5mm*5mm*5mm |
Maximum Build Size | 400mm*350mm*350mm |
Recommended wall thickness | 1.0mm |
Minimum Embossed & Engraved Details | 0.8 mm deep & 0.8 mm wide |
Minimum Clearance (between parts that will be assembled together) | 0.2mm |
Minimum Clearance (between two moving or connecting parts) | 0.6mm |
Threads Design | Thread pitch – 0.6mm |
Minimum Escape Hole Diameter | 2.5mm |
Minimum Holes design | 1.5mm |
Minimum column design | 2.0mm |
SLS Common Use Cases
SLS is best known for making parts in the ducting arena such as those used in aircraft. It excels at creating mutiples of a single geometry, low level production. Applications where there will be pressure, or fuel commonly use SLS. A small list of other applications seen in SLS:
- Complex ductwork
- Snap fit designs
- Living hinges
- Thin walled components
- Fire retardant parts
- Under-hood components
- Aerospace production parts
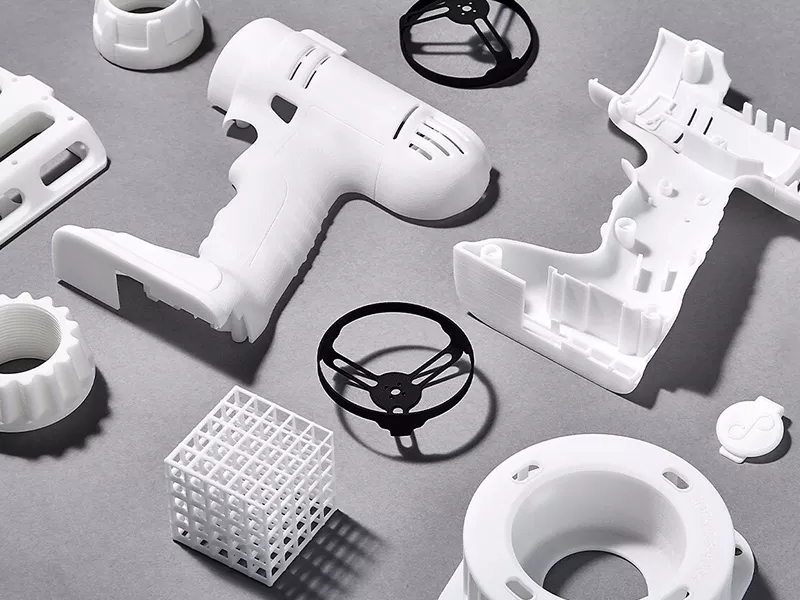
How do SLS and SLM (selective laser melting) differ?
Basically, SLS and SLM are two sides of the same coin. Both are additive manufacturing technologies that use a laser to shape powder materials into 3D objects. The main difference between the two technologies lies in the materials being processed. SLS 3D printing mainly processes plastic materials, while SLM is particularly suitable for metals. Smaller differences can also be found in the process details. In SLS, the build space and the powder are heated to just below the melting point so that the laser only has to input the remaining amount of energy to melt the powder.
In SLM, on the other hand, the build space does not heat up. Instead, it is filled with an inert gas such as nitrogen to prevent oxidation of the metal powder. Another difference lies in sintering and melting. In melting, there is a phase transition from the solid to the liquid aggregate state of the material. In sintering, on the other hand, the temperature is not high enough to melt the material completely. Instead, the material particles are agglomerated as the grain does not completely melt but heats up enough to bond with neighboring grains.
Upload Your File To Get An Instant SLS 3D Printing Quote
Our experts have a proven history of providing innovative solutions at every stage of product development—from product design through production.