Custom Die Cutting Services
Custom Manufacturing and Supplies There are many ways to produce custom die cuts. Die-cutting method is determined based on quantity and required delivery time. Not only do we offer a variety of precision die cuts, we can also provide low-cost molds and have the ability to handle any size order from 100 to 10,000,000 pieces. Upload your CAD files to get an instant quote for your die-cut parts.
Our advance flatbed and rotary die cutting capabilities with our extensive manufacturing and material knowledge will support our customers at the highest level.
We pride ourselves on quality, communications and on time delivery. Our flatbed and rotary die cutting offers low cost tooling with short lead times and tolerances to +/- .005. The strong partnership we have developed with our vendors creates a versatile selection of materials for your unique application. We also offer a wide range of specialized materials such as EMI and RFI shielding, thermal management, conductive and non-conductive, flame-retardant and UL rated materials.
Our sales, customer service and engineering team are second to none. Our team will assist you from beginning to end of your project. From prototype to large volume production runs, we can custom cut products to your requirements and specifications from a variety of non-metallic materials.
What Is Die Cutting?
Die cutting is a manufacturing process used to cut out precise shapes from materials such as paper, cardboard, fabric, leather, foam, plastic, and various other materials. It involves the use of a specialized tool called a die, which is a sharp-edged blade or a set of blades formed into the desired shape. The die is mounted onto a press, and the material to be cut is placed underneath it. When the press is activated, it applies pressure to the die, causing it to cut through the material and create the desired shape. The die can be custom-made to produce specific shapes, such as letters, numbers, logos, or intricate designs.
In addition to cutting, die cutting can also perform scoring, perforating, embossing, or debossing. Scoring creates creases or fold lines in the material; perforating creates small holes or dotted lines; embossing raises the surface to create a raised design; and debossing creates a depressed, or indented, design. Die cutting methods are most effective for high-volume, repetitive production runs due to the significant initial investment needed to acquire the die.
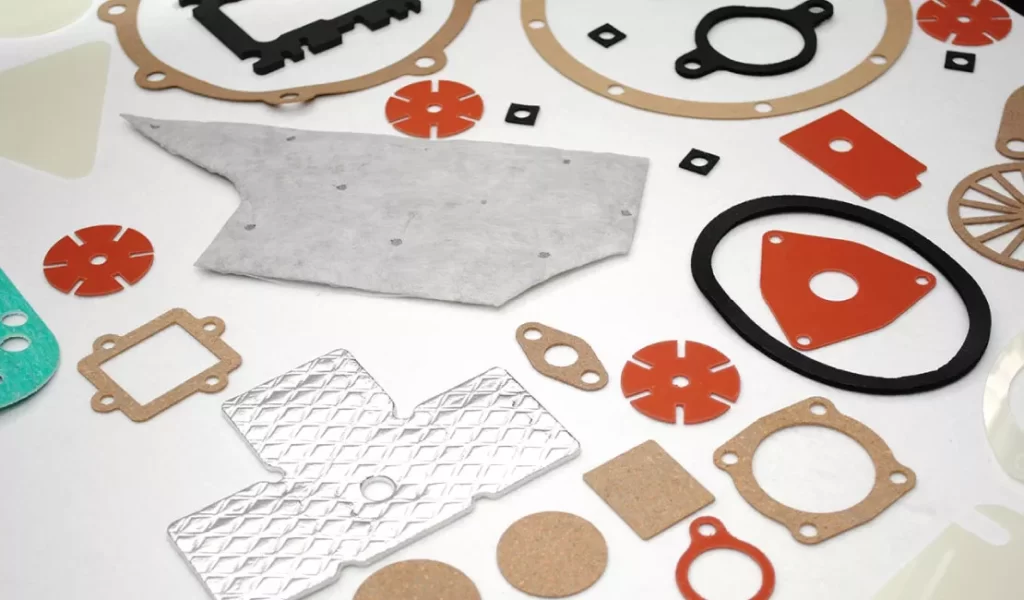
Online custom die cutting service
Rapid Manufacture provides the highest quality custom die-cutting services to meet the diverse needs of different industries and businesses. We are proud to be ISO 9001:2015 and AS9100D certified, which ensures we adhere to industry best practices. You can get a quote quickly through our online quotation system, just upload the CAD design drawings.
Die-cutting is a versatile manufacturing process that involves cutting a variety of materials into precise shapes using specialized molds. Rapid Manufacture’s custom die-cutting services offer a variety of processes and materials that provide superior precision and efficiency.
Custom Die Cutting Services
- Design Assistance – we can assist with part configuration, material and adhesive selection, and other technical considerations vital to the performance of your product.
- Prototype – we can rapidly produce prototype parts for actual functional testing.
- Short or Long Run Production – based on your requirements, we are highly efficient in both short and long runs.
- Quality Control – from raw material inspection to finished product, we maintain tight quality control to insure compliance to specifications.
Types of Die Cutting Processes
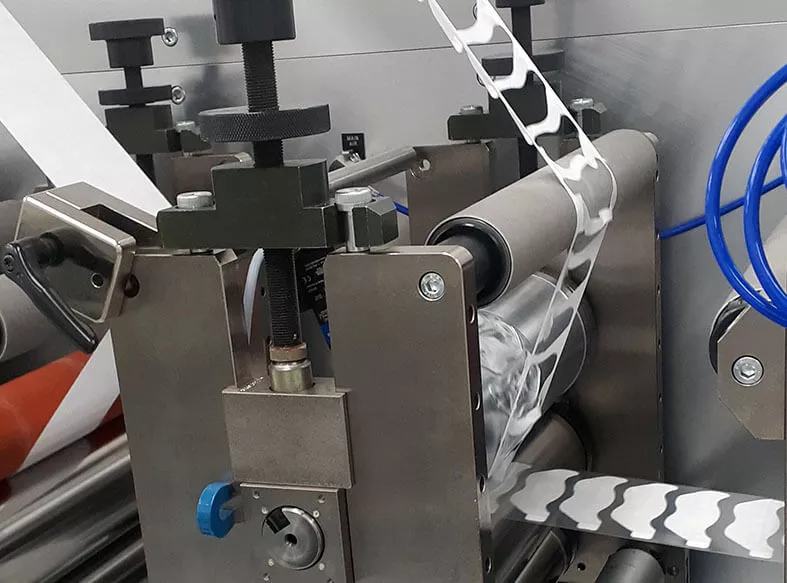
Rotary Die Cutting
In rotary die cutting, the material is passed between a cylindrical die and an anvil roll. The die is cylindrical and rotates at a high speed, while the anvil roll provides support. This process allows for quick and efficient cutting of materials, as an entire sheet or web of raw materials can be fed into the press at once. Once the machine is loaded, it can cut various shapes and designs with ease. Rotary die cutting services are often used for high-speed production of labels, stickers, and intricate designs.
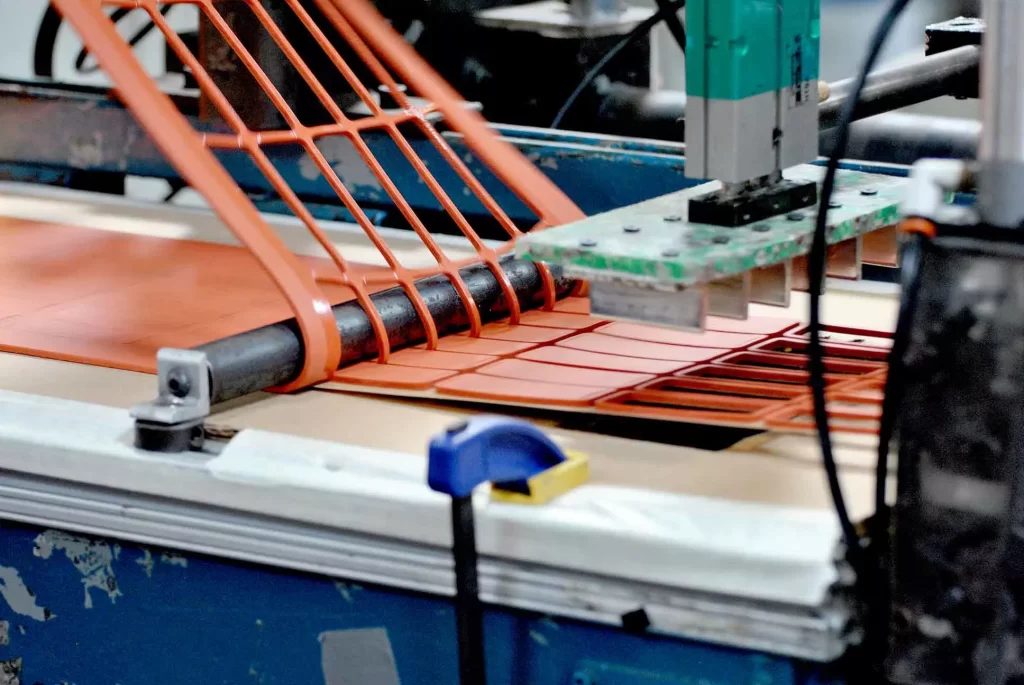
Flat Bed Die Cutting
The most common die cutting process is known as flatbed die cutting or steel rule die cutting. This process involves the use of a flatbed die cutting press and steel dies to accurately cut raw materials into custom shapes and designs. It is especially effective for cutting thicker materials (more than ⅛ inch in thickness), thanks to its ability to apply significant pressure. The pressure capabilities of flatbed die cutters can vary depending on the specific machine and its design. For example, some flatbed die cutters may have pressure capabilities ranging from a few tons (e.g., 2-5 tons) up to larger machines capable of exerting 20 tons or more. These higher-capacity machines are often used in industrial settings for cutting heavy-duty materials or for high-volume production. Flatbed die cutting is highly advantageous for short production runs, as it can operate in semi-batch or batch production modes. It is versatile and suitable for cutting a variety of materials, including paper, cardboard, foam, fabric, and plastics.
Materials used for die cutting
Rapid Manufacture works with some of the industry’s top suppliers to offer the most cost-effective, highest-quality raw materials for your die cutting requirements. Our ISO 13485 certification and 3M Preferred Converter status exemplify our dedication to superior quality and service. We can also work with customer-supplied materials for many of our die cutting applications.
- Paper
- Foam
- Tape and adhesive
- Foil
- Film and plastic
- Fabric and mesh
- Rubber
- Nonwovens
- Thermal management
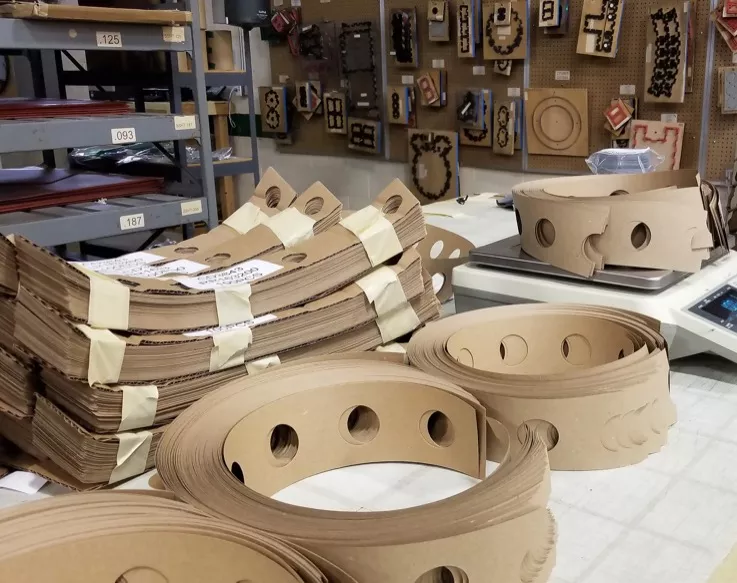
Die Cutting Advantages
Die cutting offers several advantages, making it a popular manufacturing process in many industries. Here are some key advantages of die cutting:
- Affordability
- Customizable
- Flexibility and Versatility
- Precision and Accuracy
- Automation and Integration
Die Cutting Disadvantages: May Not Work With Thick Material
Die cutting is most effective for materials that are relatively thin and flexible. Thicker materials, such as thick cardboard or metal sheets, may pose challenges in achieving clean and precise cuts. The thickness of the material can make it difficult for the die to penetrate and cut all the way through the material, resulting in uneven or incomplete cuts.
The maximum thickness of material that a die cutter can handle depends on several factors, including the specific machine model, its design, and the type of material being cut. While die cutters are generally capable of cutting a range of materials, including thicker ones, there are limitations to consider.
Most flatbed die cutters are designed to handle materials of moderate thickness, such as paper, cardboard, thin plastics, and fabrics. These machines can typically handle material thicknesses ranging from a few millimeters to around 6-10 millimeters, depending on the specific model. The maximum thickness that can be effectively cut will depend on the machine’s cutting force, the type of cutting tool being used, and the machine’s overall design and capabilities.
In general, if you’re working with materials thicker than what a standard flatbed die cutter can handle, you may need to consider alternative cutting methods specifically designed for thicker materials.
We work with every industry
Rapid Die-Cut is versatile and we have experience fabricating custom parts out of thousands of different engineering-grade materials. We can work within the tightest tolerances, quality and speed with go to market in mind.
Alternatives to Die Cutting
While die cutting is a widely used manufacturing process, there are alternative methods available for achieving similar outcomes here at Rapid Manufacture. Here are some alternatives to die cutting:
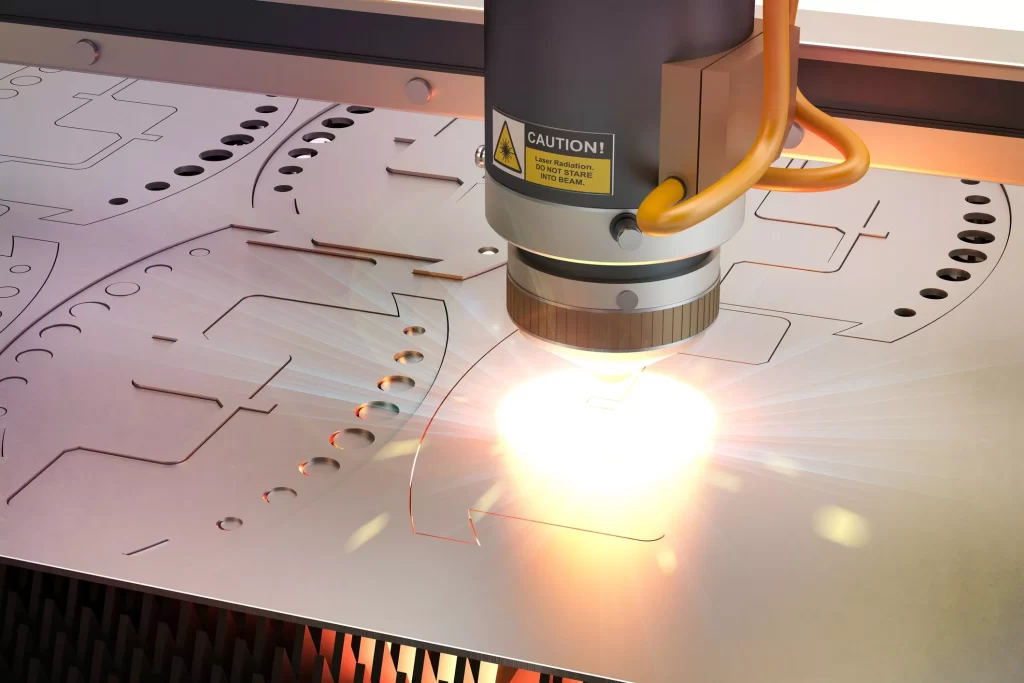
Laser Cutting
Laser cutting utilizes a laser beam to precisely cut through materials. It offers high precision, intricate detailing, and the ability to cut a wide range of materials, including plastics, wood, acrylics, fabrics, and metals. Laser cutting is particularly suitable for thin and delicate materials or designs that require high levels of complexity.
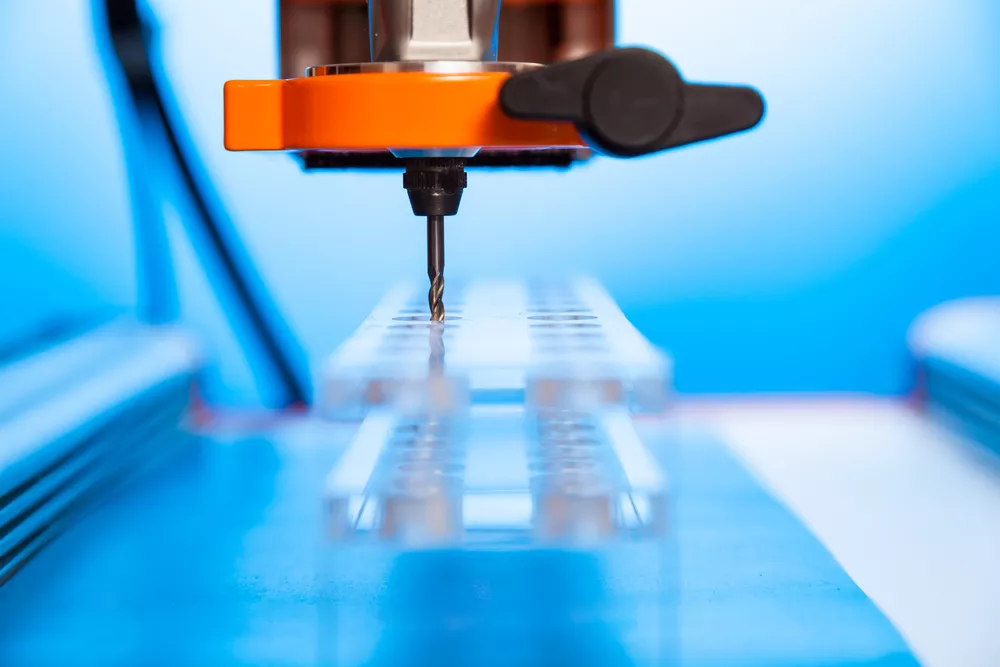
CNC (Computer Numerical Control) Routing or Milling
CNC routing and milling involve the use of a computer-controlled machine with cutting tools to carve, shape, and cut materials. It is suitable for materials like wood, plastics, foams, and nonferrous metals. CNC routing offers high precision, versatility, and the ability to create complex 2D and 3D shapes.
Ready to work with the Rapid Manufacture team?
Stand out from the competition by collaborating on your next die-cutting project with Rapid Manufacture. From rounded corners to intricate designs, the Rapid Manufacture team is ready to help! Upload your CAD design drawings through the online quotation system immediately and let’s discuss digital die cutting.