Medical parts, components, and equipment manufacturing
Medical device prototyping and rapid manufacturing are the foundation of your medical product design and development process. You can send these prototype parts and low-volume production parts to the lab or clinical trials and ultimately to market faster.
Why work with us?
With a higher demand for quality, precision, and safety than any other industry, the medical industry is responsible for lives. Today’s medical devices are more personalized and patient-focused than ever before with our on-demand manufacturing capabilities and engineering expertise. At Rapid Manufacture, we utilize our wide range of custom manufacturing services, including CNC machining, injection molding, or a combination of manufacturing methods, to ensure we can exceed our customers’ unique requirements. We have been working with medical device companies, from start-ups to Fortune 500, with many complex applications. We also provide the perfect solution for medical-grade materials for physicians, patients, research institutions, and medical students.
Rapid prototyping
We can shave months off development timelines with rapid iteration of production components to quickly arrive at an optimized design.
Production capacity and flexibility
Rapid Manufacture delivers quick-turn part production, making it easier to respond to sudden increases in demand or supply chain disruptions.
Technology-agnostic manufacturing
We offer the processes and biocompatible materials needed to make medical device applications, from wearables to surgical devices and capital equipment.
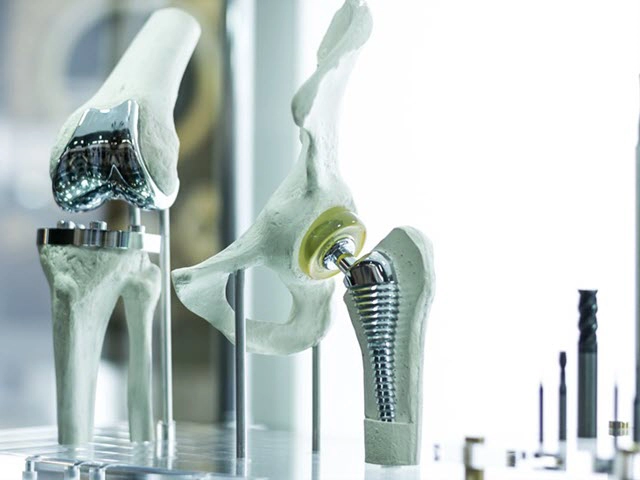
Accelerate time to market
Prototyping and rapid manufacturing are essential for medical device development
The design and development of new medical devices is both an expensive and time-consuming project. However, prototyping and rapid manufacturing allow outstanding innovators to redefine best practices from concept to commercialization, enabling you to bring your new medical device to market efficiently and cost-effectively.
Rapid prototyping manufacturers can quickly, consistently, and cost-effectively deliver prototypes with basic functionality and production parts manufactured in small batches for concept and market testing of medical devices and healthcare products. This allows you to explore ideas, generate early customer feedback and develop fit-for-purpose solutions to put them into lab or clinical trials and ultimately bring them to market faster. You also gain insight into subsequent manufacturing processes, costs, schedules, and quality control.
Evaluate, test and validate your every step
Best Practices Supported By Medical Device Prototyping And Manufacturing
Build product ideas of medical devices into a manageable scope while working to establish the critical details and fully understand the design intent through proof-of-concept prototypes.
Visual presentation models empower designers to share the appearance and aesthetics of their designs with colleagues, clients, and stakeholders to facilitate the clear and actionable feedback.
The medical device functional prototype development (also refered to as Beta prototype) can be used to test the form, fit, and function of parts to refine design iterations and product performance, let any issues to be discovered and corrected well before getting to a final product, and reduce business risk.
Creating engineering prototypes of medical devices that match final product makes it easier to verify design, engineering, and manufacturability before investing in expensive tools and putting them into production.
Rapid manufacturing of medical devices and custom low-volume production will be able to bridge the gap between prototype and production, and make your product go to market faster at an affordable price.
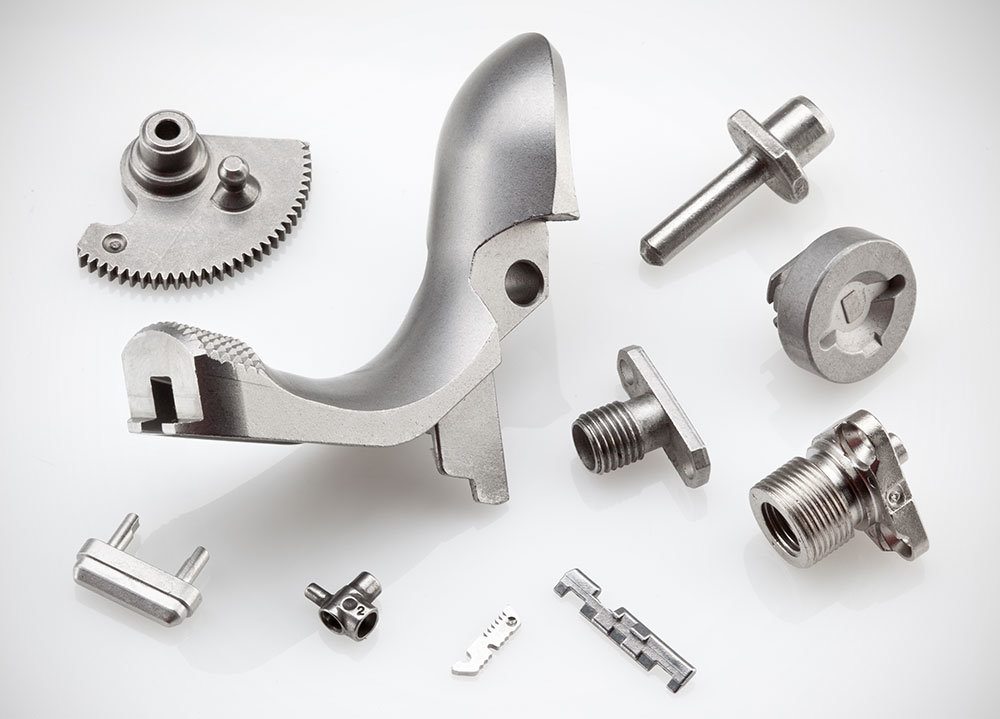
What Materials Work Best for Medical Applications?
- High-temp Plastics. PEEK and PEI (Ultem) offer high-temperature resistance, creep resistance, and are suited for applications that require sterilization.
- Medical-grade Silicone Rubber. Dow Corning’s QP1-250 has excellent thermal, chemical, and electrical resistance. It’s also bio-compatible so can be used in applications that require skin contact.
- Carbon RPU and FPU. Carbon DLS uses rigid and semi-rigid polyurethane materials to build functional parts ideal for late-stage prototyping or end-use devices.
- Micro-resolution. MicroFine™ (green and gray) is a proprietary material developed by Protolabs to build complex 3D-printed parts with micro-sized features as small as 0.0025 in.
- Microfluidics. Watershed (ABS-like) and Accura 60 (PC-like) are clear materials can be used for microfluidic parts and transparent components like lenses and housings.
- Medical Alloys. Between machined and 3D-printed metals along with sheet metal, there are more than 20 metal material options available for medical components, instrumentation, and other applications. Metals like titanium and Inconel have attributes like temperature resistance while various stainless steel materials brings corrosion resistance and strength.
Medical Device Manufacturing
The medical industry depends on accurately and precisely created products to safeguard human health. Our ISO 13485 certification shows that we deliver precise, high-quality medical components that meet regulatory and quality standards. Enjoy reliable and professional medical device manufacturing solutions for custom products with the highest quality standards.

We Are ISO 13485 Certified!
Rapid Manufacture boasts the ISO 13485 certification, a management systems standard designed for medical device manufacturing. This shows that all the medical device prototypes and components you get from us meet adequate regulatory compliance. It also demonstrates our quality control and assurance system, assuring you that we will manufacture components to your specific needs. We are ready to serve every client in the dental, biotechnology, surgical, and pharmaceutical industries and more.
Precision Medical Applications
- Medical Wearable Devices
- Surgical Training Models
- Dental Implant Devices
- Orthopaedics Model
- Enclosures and Housings
- Ventilators
- Prosthetic Components
- Scientific Equipment
- Medical Trolley
- Medical Monitor Instruments
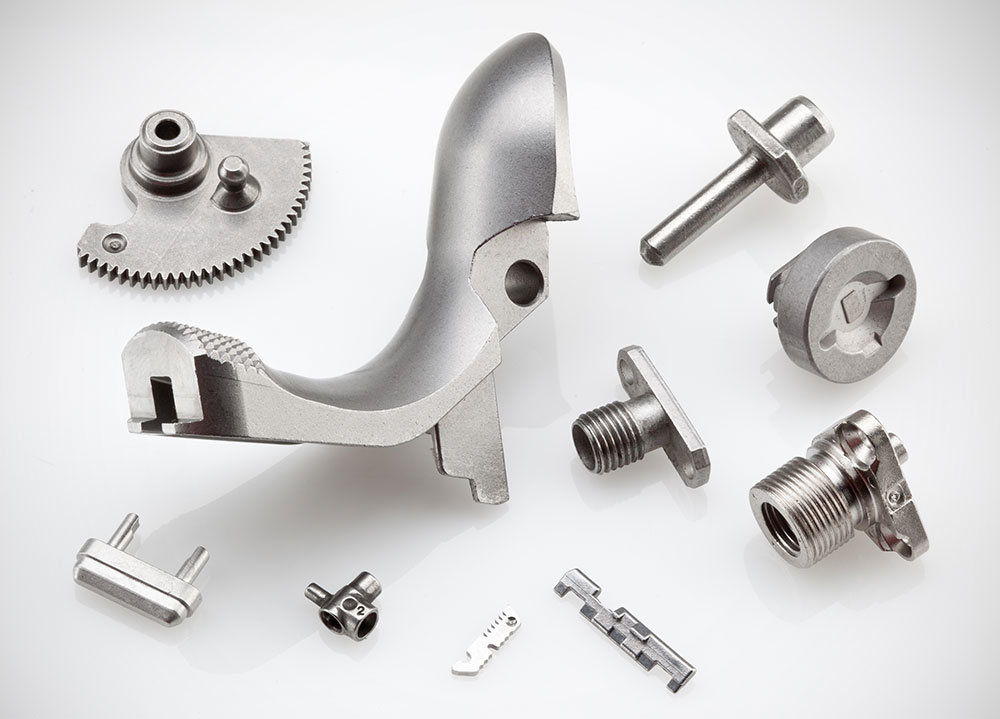
Custom Prototypes and Parts for Medical Devices Industry
Several leading medical device companies depend on our outstanding medical prototyping and production solutions for their custom medical parts. Our manufacturing capabilities and quality management system ensures that we produce components that meet performance and safety standards.
Explore More Industries We Support
Years of serving various clients gave us the experience and knowledge needed to support numerous industries. Click on the link below to know more.
Let's Start A New Project Today
Get to market faster and streamline your supply chain with rapid prototyping and on-demand production of medical components