Die Casting
Consistent, reliable, and fast production for small-to-medium sized parts
Die Casting Services
Rapid Manufacture dies casting services offer high-output production capacity, low cost, and flexible part design options making it an appealing casting choice for non-ferrous metal products. Our die casting facilities are equipped to handle a variety of designs, materials, and manufacturing needs across multiple industries.
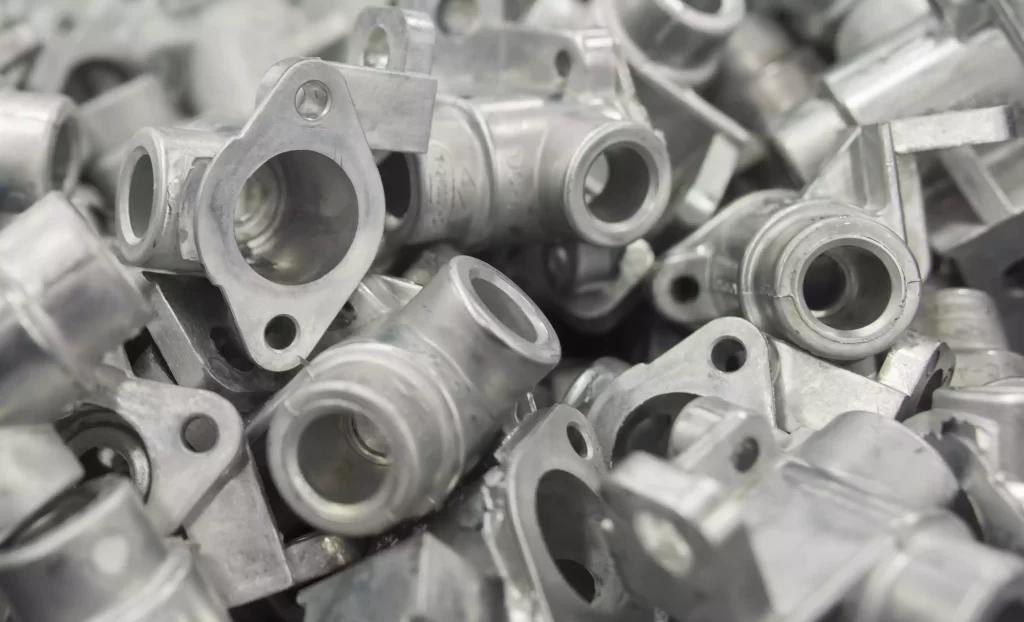
Die Casting Services Instant Quotation
As a tech-driven die casting company, we have developed AI powered quotation platform that simplifies your ordering and manufacturing process.
Rapid Manufacture’s die casting service process
Start A Quote
Upload your files to the Rapid Manufacture Quote Engine and configure your project. Our team will consult with you to ensure your specifications, lead time, and price fit your project needs. We will provide a DFM report for approval before kicking off tooling.
Sample Approval
Once your project is kicked off we will build a high-quality die. After the tooling is created we will send out part samples, called T1s, for approval.
Production starts
Once we're satisfied with your sample, we move forward with production and delivery of the part. Rest assured, Rapid Manufacture is handling production management and logistics throughout the entire process. You own your tools and can easily reorder them as needed to meet your needs.
Is Die Casting Right For Your Product?
The die casting process is the fastest option available for producing exact, non-ferrous metal products. Because this method utilizes reusable molds, it offers high-speed production of parts and has the flexibility to create a wider range of shapes and sizes than other casting methods.
Die casting can be completely automated, and its reusable molds also make it an affordable option. This technique is used to manufacture commercial, consumer, and industrial products. Die casting is ideal for medium-sized parts with more complex structures.
When looking for fast large-scale production of parts without sacrificing detail and surface quality, die casting is a perfect manufacturing option.
State-of-the-art Die Casting Facilities
- 11,000 sq. ft. in China
- 30 die casting machines for aluminum, magnesium, and zinc
- Quality system: ISO 9001:2000
- Die casting machines tonnage sizes: 150-2,500 ton
- Die casting alloys casted:
- Magnesium die casting: AZ91D, AM60B
- Aluminum die casting: ASTM: A356, A360, A380, A383; JIS: ADC1, ADC3, ADC6, ADC10, ADC12
- Zinc die casting: Zamak 3, Zamak 5, ZA8, ZA27
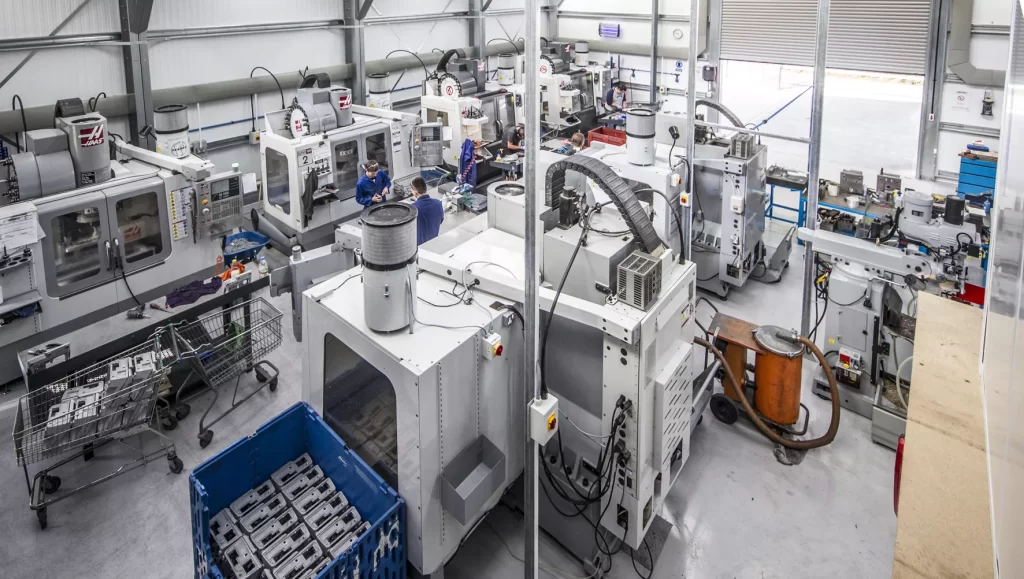
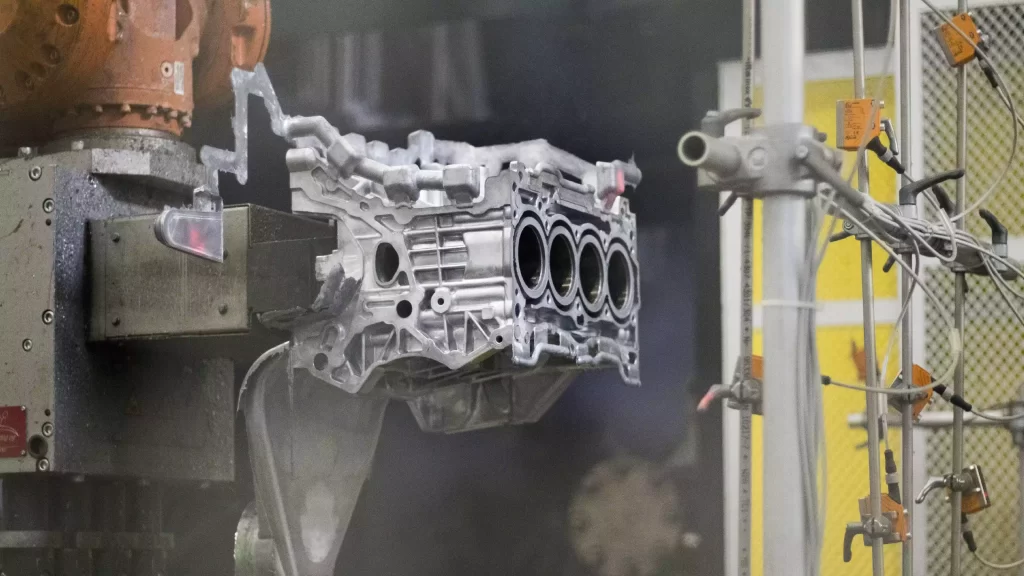
The Pressure Die Casting Process
The success of your high pressure die casting project depends on the quality of the mold tools, and our tool making abilities are unmatched in Asia. After we receive your order, we will:
- Perform a complete Design for Manufacturing review of your CAD files.
- Verify tooling and product raw materials for compliance.
- Use our multi-axis imported CNC machine tools to fabricate the core and cavity.
- Apply careful heat treating to temper the molds.
- Exercise process control when casting your parts.
- Provide any necessary post-machining or processing.
- Professionally inspect and measure finished parts to meet and exceed your specifications.
Advantages Of Pressure Die Casting
Highest Rate of Production
Die casting is the fastest way to turn your prototype into production, providing the highest rate of production for traditional manufacturing services.
Durable and Stable
Parts produced through die casting service are made from metal, meaning they are more durable and stable than those made from plastic injection molding.
Consistently Identical
With a reliable mold, die casting service can produce thousands of consistently identical castings with specified tolerances without additional tooling.
Die casting materials and metal alloys
Rapid Manufacture’s Die-casting services encompass three major material types – zinc, copper, and aluminum.
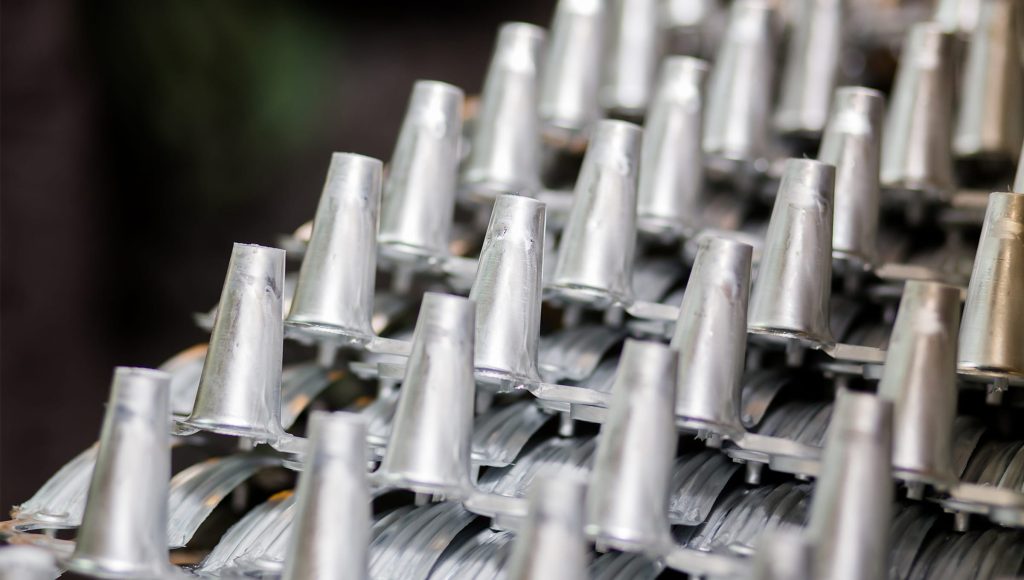
Zinc Die Casting
Zinc is a heavier metal that provides robust characteristics to die cast parts. It offers a unique combination of impact strength, resistance to catastrophic failure, and ductility, making it a good choice for a wide range of applications.
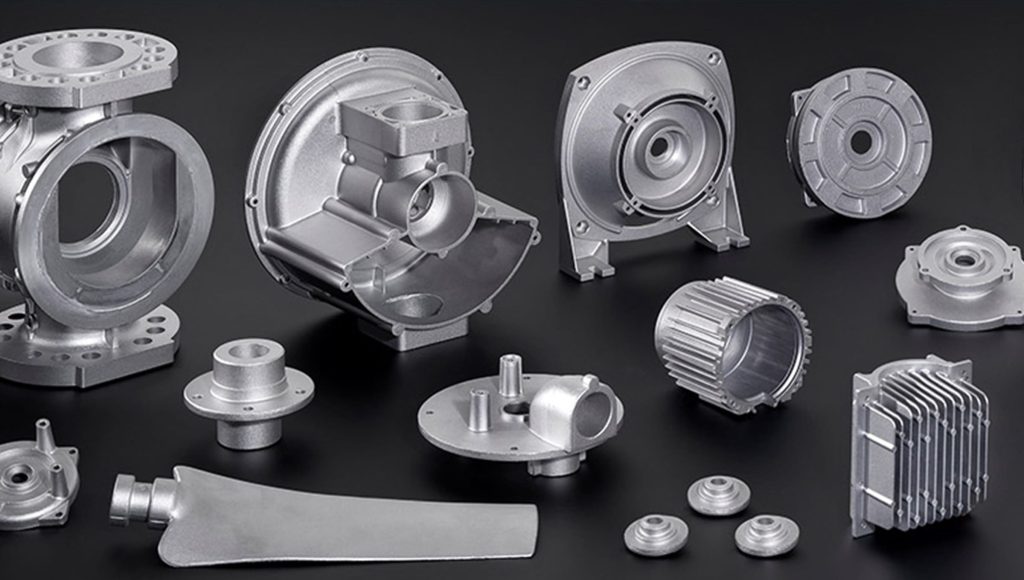
Aluminum Die Casting
Aluminum is among the most popular metals used for die casting due to its ability to handle high temperatures while maintaining strength and lightweight. Aluminum die-casts are conductive and corrosion-resistant.
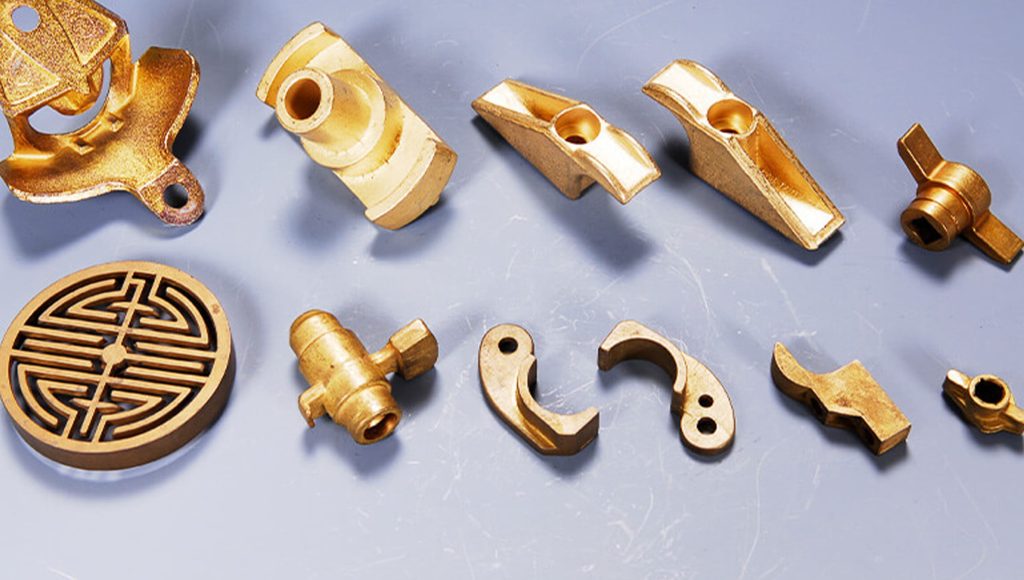
Copper Die Casting
Copper is considered a specialty metal for die casting. Copper casted parts are prized for their high mechanical properties, resistance to wear, high hardness, and strength close to that of steel parts.
Die Casting Surface Finishes
Post-processing and finishing is the final step of precision die casting. Finishing can be applied to remove the surface defects of cast parts, enhance mechanical or chemical properties, and improve products’ cosmetic appearance. There are six types of die casting surface finish options.
As Cast | Regular casting finish obtained without the use of high-end tools or machinery. Like Zinc and Aluminum-Zinc parts can be as cast but still keep high corrosion resistance. | All materials | n/a | n/a | / | |
![]() | Powder Coating | Powder coating can be used to spray a free-flowing, dry powder to the zinc alloy and aluminum alloy die casting. Under strong electrostatic and high temperature, the powder will be uniformly adsorbed on the surface of the casting, forming a powder layer that can mask defects very well. | Aluminum, Stainless Steel, Steel | Black, any RAL code or Pantone number | Gloss or semi-gloss | Learn More>> |
![]() | Bead Blasting | Bead Blasting is a process that sprays fine glass beads at high speed onto the surface of die casting parts using compressed air as the powder. The appearance or shape is changed, and the part obtains excellent cleaning and surface preparation for secondary finishing operations. | ABS, Aluminum, Brass, Stainless Steel, Steel | n/a | Matte | Learn More>> |
![]() | Anodizing | Mainly for aluminum alloy die casting. Anodizing utilizes electrochemical principles to generate a layer of Al2O3 (aluminum oxide) film on the surface of the parts. This decorative layer of oxide film provides high insulation and wear resistance. | Aluminum | Clear, black, grey, red, blue, gold | Smooth, matte finish | Learn More>> |
Electro Phoresis | Used for aluminum alloy, zinc alloy die casting, etc. Electrophoresis applies metallic luster and an unlimited range of colors on the casting parts. It also can enhance the surface properties and corrosion resistance of metal alloy parts. | Aluminum, Zinc, Stainless Steel | Any | Metallic luster | / | |
![]() | Electroplating | Electroplating can be functional, decorative or corrosion-related. Many industries use the process, including the automotive sector, in which chrome-plating of steel automobile parts is common. | Aluminum, Steel, Stainless Steel | n/a | Smooth, glossy finish | Learn More>> |
![]() | Brushing | Brushing is a surface treatment process in which abrasive belts are used to draw traces on the surface of a material, usually for aesthetic purposes. | ABS, Aluminum, Brass, Stainless Steel, Steel | n/a | Satin | Learn More>> |
Our Die Casting Serves Nearly All Industries
Rapid Manufacture works with leading manufacturers from different industries to support growing demands and streamline their supply chain.