Compression Molding Services
Rapid Manufacture: Compression Molding Services
Our teams of compression molding specialists use advanced equipment to create components of various sizes, weights, and materials for projects of all sizes, from a few prototypes to large-run production jobs.
Our compression molding equipment is constantly at work creating numerous products including: lightweight fiber dash insulators, molded cargo management systems, trunk trims, cast foam dash insulators, and others.
We also offer injection molding services which differ from compression molding in that plastic is melted and injected into a molding tool. This process is commonly used to produce small-to-mid-sized orders of plastic components.
Rapid Manufacture is a compression molding company, so you can trust that our compression molding engineers and designers have extensive experience taking traditional sheet metal or aluminum components and redesigning them as lightweight composite components. Often times we are able to take an assembly with 20 different part numbers and compression mold it as a single finished component. Our team of compression mold manufacturers have begun to mold in complex ribs and attachments for cost and weight savings while completely eliminating the need for secondary assembly.
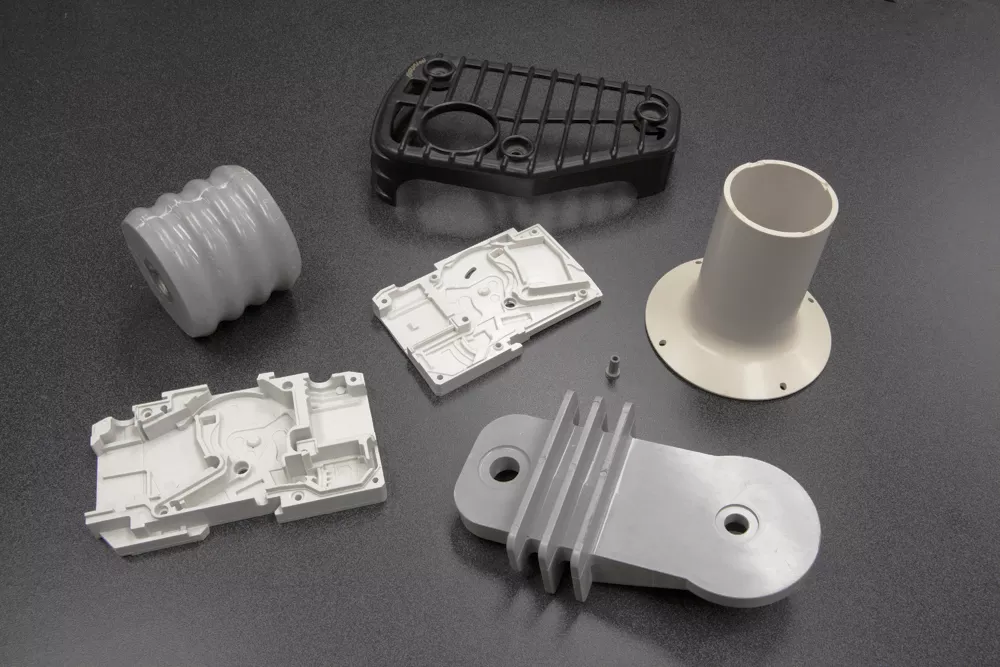
Who Needs Compression Molding Services?
Compression molding services are an ideal process for large, complex parts that require high strength and stiffness. The compression molding process can be used to mold parts with a wide range of size, shapes, and complexity. Compression molded composites are also known for their superior dimensional stability, making them ideal for applications where close tolerance is required.
Compression molding tooling is typically less expensive than tooling for other processes and can be quickly produced. Our team of compression molding experts has the experience and knowledge to produce high-quality, complex parts quickly and efficiently.
Get a compression molding quote online
Our customer-first approach means our manufacturing facilities will compression mold parts just the way you need them, at the right price, without having to compromise on design. We provide expert consultation with every injection mold quote and a project manager with every order to move your part from design to production.
Introduction to Compressing Molding
Compression molding is a forming process that heats and softens a plastic material to achieve the desired shape. It entails placing the plastic material into an open, heated metal mold, either in the form of pellets or sheets. The mold then softens the material, forcing it to conform to the mold’s shape as pressure is applied while it closes, allowing the curing phase to take place. Once completed, the operator can remove excess materials protruding from the mold, called “flashes,” to achieve a good finish.
First developed to manufacture composite parts for metal replacement applications, the typical usage of compression molding is to make larger flat or moderately curved parts for the automotive industry, including Long Fiber Reinforced Thermoplastics (LFT) and Glass Fiber Mat Reinforced Thermoplastics (GMT). Some of these parts include: hoods, fenders, scoops, spoilers, and smaller, more intricate parts.
One main advantage of compression molding is its capacity to mold large, relatively intricate parts as well as to produce ultra-large basic shapes that would otherwise be impossible with extrusion techniques. It is also one of the lowest-cost methods compared with transfer or injection molding. Plus, waste reduction is maximized, which is particularly beneficial when working with expensive compounds. The drawbacks of compression molding include poor product consistency, difficulty in controlling flashing, and its lack of suitability for certain types of parts.
Compression molding can manufacture based on numerous materials such as polyester fiberglass resin systems like Bulk Molding Compound (BMC) or Sheet Molding Compound (SMC), polyamides imides (like Torlon), polyimides (like Vespel), PolyPhenylene Sulfide (PPS), PolyEther Ether Ketone (PEEK), phenolics, thermoset polyester vinyl ester, epoxy, Diallyl Phthalate (DAP) and silicones.
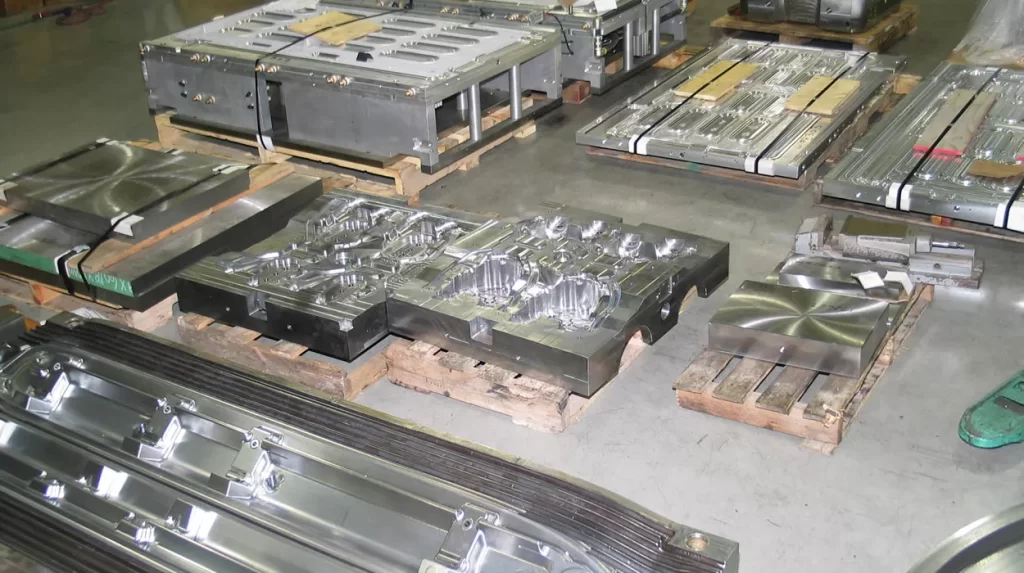
The benefits of compression molding include:
Product uniformity
Compression molding allows for part geometry and configurations not achieved by other casting methods.
Dimensional stability
Compression molding is ideal for applications with tight tolerances and low durometer.
Cost-effective process
With compression molding, secondary operations, such as grinding or finishing, are often not needed.
Material choice
Urethane Innovators is adept at compression molding a wide range of urethanes, rubbers, and silicones.
Materials and Composites
- KEVLAR
- AZDEL
- PET (POLYETHELENE TEREPHTALATE
- GMT (GLASS MAT THERMOPLASTIC)
- EVA (ETHYLENE VINYL ACETATE)
- INSULATION/ FOIL
- S-GLASS
- E-GLASS
- SMC- SHEET MOLDED COMPOUND
- CHOPPED CARBON FIBER
- CARBON FIBER PRE-PREG
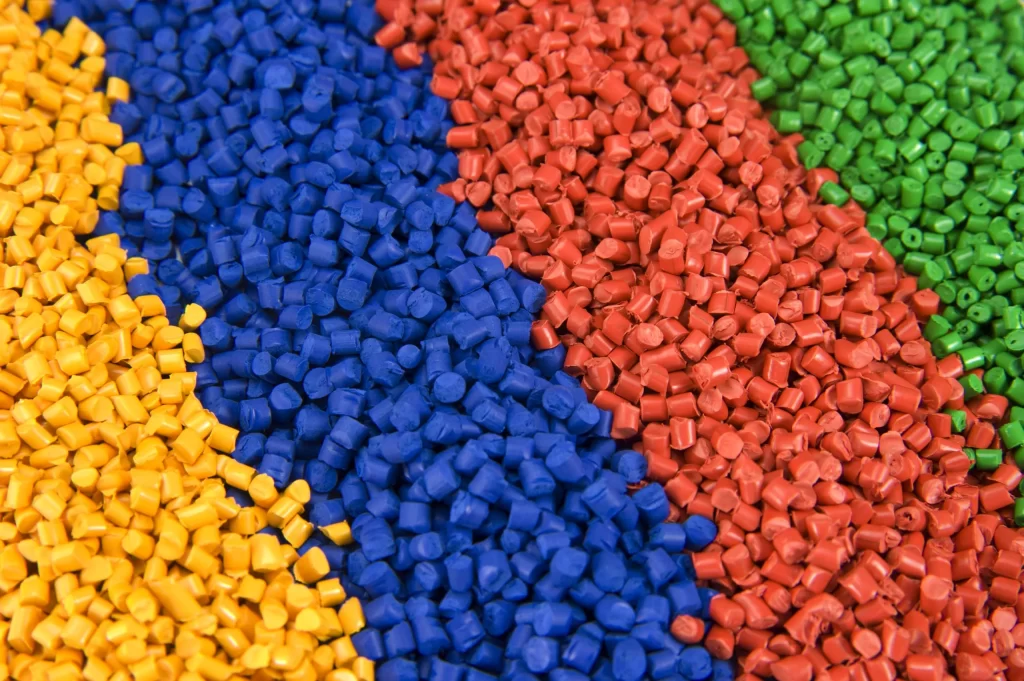
We Work With Nearly All Industries
Rapid Manufacture’s Compression Molding Services is perfect for addressing the various demands of different industries, including the automotive, medical, and consumer goods fields.
Our in-house development and highly qualified team of engineers are what we have to offer you!
Successful injection molding simulations require a direct connection between the user and a competent engineering team. Therefore, our solution services, customer support, and other groups will work closely with you to help you succeed!